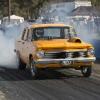
Fluid filled harmonic balancers
#1
Posted 06 March 2010 - 07:56 PM
im after some information on where to find/make a fluid filled damper to suit a holden six.
I know that the commonly used one was off a Massey Ferguson tractor and one off a Massey Ferguson crop Harvester. Also heard of a perkins tractor balancer being used too?
How do they fit? do they bolt onto a standard holden balancer or do they have a bush pressed and welded in and outside of the part that goes into the timing cover (forget what its called) turned down to suit the holden timing cover seal?
I know Harrops Howler ran one the size of a flywheel and i think Jim Rowleys Duel torana ran one as well?
any leads or information would be great.
Kevin
#2
Posted 06 March 2010 - 11:41 PM
I don't know any appropriate floating hub balancers that are easy to get your hands on, but I intend to find out. You need something good if you're spinning it out hard, but a floating hub unit isn't great for clearance!
#3
Posted 07 March 2010 - 07:03 AM
Edited by warrenm, 07 March 2010 - 07:08 AM.
#4
_oldjohnno_
Posted 07 March 2010 - 07:59 AM
Is there some reason you want to use the Perkins balancer in particular? Authenticity for a nostalgia car perhaps? If not then I think there are now alternatives that will work at least as well (and probably better) than the Perk job.
You have to remember that back then there wasn't much available so people just had to adapt what was at hand.
The fluid balancers were thought to be a good thing because they didn't have their own resonant frequency and would work to some extent on any engine and at any speed. They probably aren't the best choice for high rpm work though; they seem to work best on low frequency applications like diesels. I think balancers from V8 Dodges were also adapted.
If you do decide to use a fluid filled balancer (eg Fluidampr) be careful how you handle it. Too much heat (from welding in a sleeve for eg) can balloon them and the outer shell is thin so you have to be careful how you chuck it in a lathe so as not to lock the shell onto the inertia ring. I tend to think the elastomeric and the pendulum types are a better choice for what we are doing anyway. A rough rule of thumb is that anything you do to reduce the difference in the moment of inertia between the balancer and flywheel will tend to reduce the torsional vibrations. So increasing the balancer diameter will have as much or more effect as just making it heavier - 7 to 8" should be about the minimum if you're gonna spin it up. I'm using a big-block Chrysler Rattler on a 202 I'm building ATM but I think the ATI elastomer units would work very well too. They have o-ring style rubbers that are replaceable/tunable so should be able to be made work well at whatever speed you run. With the bigger dampers like these you could probably machine the nose right off and just bolt the balancer to a machined hub that fits onto the crank snout. The hub would fit into the front seal and have a drilled and tapped flange on the front to take the balancer.
If you check out the Powerbond website they have pdfs that show all the dimensions of their range. Most will be too small though. Also on the TCI site you will find dimensions for their range. I'm sure you'll find something that will work well and can be adapted fairly easily.
#5
Posted 09 March 2010 - 08:50 PM
http://www.fluidampr.com/CHEVROLET.htm
An 8 inch bbc one, bolted to my standard looking Powerbond balancer.
although i would drill and tap the balancer and have 6 7/16 bolts and loctite to hold it together.
Of course, it could be out of balance so could a machine shop fix that up
Bad idea?
#6
_Bomber Watson_
Posted 09 March 2010 - 10:02 PM
I had an even stupider idea the other day, why not bolt two Holden balancers together face to face?? Would that achieve anything?
Cheers.
Cheers.
#7
Posted 10 March 2010 - 12:01 AM
why not bolt two Holden balancers together face to face?? Would that achieve anything?
Possibly a hole in the bonnet unless they were spigoted together?

#8
Posted 10 March 2010 - 07:50 AM
#10
_oldjohnno_
Posted 11 March 2010 - 06:39 AM
thinking about using one of these.
http://www.fluidampr.com/CHEVROLET.htm
An 8 inch bbc one, bolted to my standard looking Powerbond balancer.
although i would drill and tap the balancer and have 6 7/16 bolts and loctite to hold it together.
Of course, it could be out of balance so could a machine shop fix that up
Bad idea?
It would work but it's not the best way to do it. Just bolting the big balancer to the front of the little one results in a fair amount of overhung load on the skinny little Holden crank snout (though the sbc snout isn't much bigger). I know it sounds like nit-picking but I remember Brabham writing about some of the early, heavy-flywheeled GP cars. Just spinning out on a corner was enough to snap the end of the crank off due to gyroscopic forces... and any crank flex at high speeds would be magnified out at the balancer.
Ideally you would replace the little balancer altogether and try to position the new one as close to the timing cover and front journal as possible. I don't know of any balancer with a big enough recess to take a Holden hub but you could easily get a hub machined to suit a modified aftermarket balancer. The big block Chrysler balancers for example (and I'm only picking this cos I've got one handy, I'm sure others would be OK too) has about a 3" dia recess and already has a 6 hole pattern that could bolt to the adaptor. Of course the back side of the balancer recess - the bit that slips onto the crank and into the seal - would have to be faced off flush first, and I'd leave a shoulder or spigot to locate it accurately.
As far as I know it's not practical to balance the Fluidampr style units on a conventional balancing machine. The floating ring tends to settle a bit off centre and it'll show up as unbalanced. On the actual engine though the rotation speed and a bit of vibration soon jerks it into line. So long as the machining is reasonably accurate and total runout is held within a couple of thou there will be no need to balance it. Just go easy on the lathe chuck key - you dont want to crimp the casing to the floating ring.
Didn't someone here do the double Holden balancer thing?
If I understand it correctly flywheel and balancer effect is in direct proportion to mass, but varies with the square of diameter. In other words if you double the weight of a wheel you double its effect, but if you double its diameter its effect is x 4.
#11
_Bomber Watson_
Posted 11 March 2010 - 08:15 PM
Cheers.
#12
Posted 11 March 2010 - 08:25 PM
#13
_Bomber Watson_
Posted 11 March 2010 - 08:31 PM
But im toying with ideas, and thinking about seeing how much grunt i can get out of one for the least possible amount, have most the stuff i need collected, and was looking at the pile of 8 standard balancers thinking hmmmm...
Cheers.
0 user(s) are reading this topic
0 members, 0 guests, 0 anonymous users