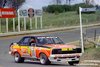
Polishing aluminium
#101
Posted 28 March 2008 - 01:44 PM
Mate that looks UNREAL! One day i will buy myself all the right tools and give it a shot!
#102
_greenmachine215_
Posted 28 March 2008 - 07:33 PM
MRLXSS: 500 is a good DEPOSIT,
i Dont have anything special, just a bench grinder with buffs, sand papers,and dremels
thanks fellas

#103
_Bomber Watson_
Posted 28 March 2008 - 08:20 PM
#104
_Viper_
Posted 28 March 2008 - 08:33 PM


Edited by Viper, 28 March 2008 - 08:33 PM.
#105
_j7723_
Posted 29 March 2008 - 08:24 AM

#106
_Viper_
Posted 30 March 2008 - 12:14 PM

My Custom remote shifter for the Gem... Heres the finished product:
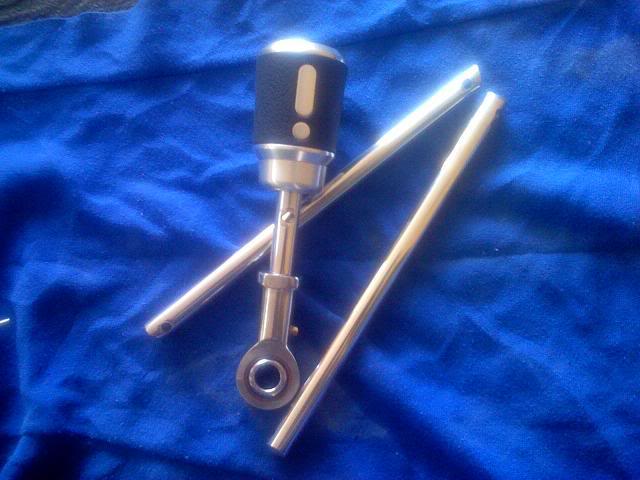
And A couple Of before and after shots:
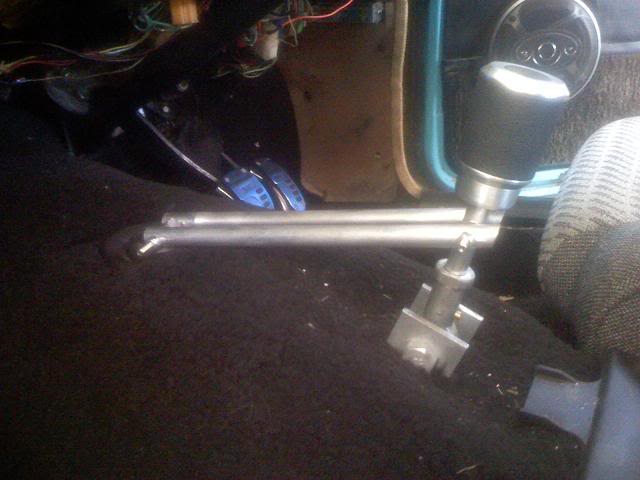
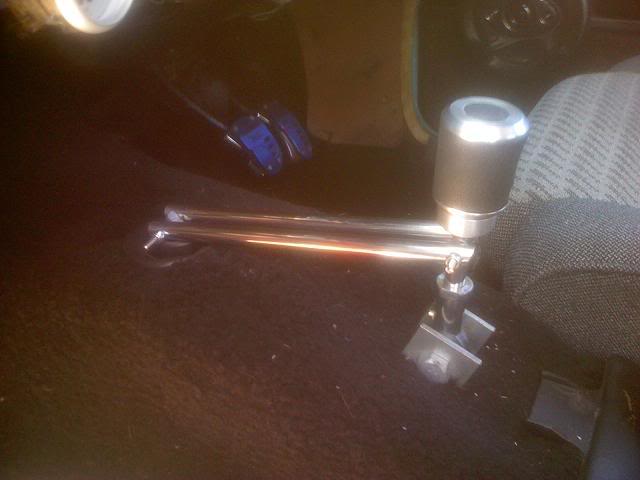
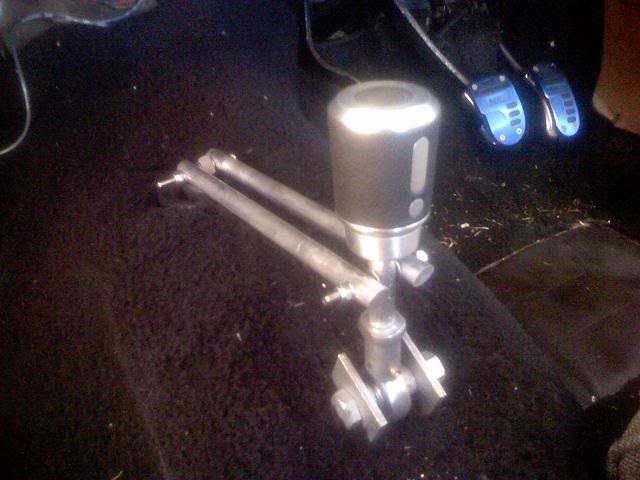
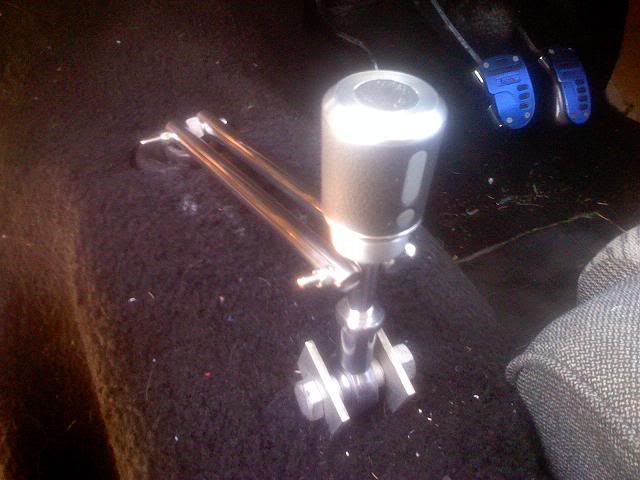
My new alloy intake manifold for the gem should Arrive this week.. Ill give that a shot

#107
_greenmachine215_
Posted 30 March 2008 - 12:46 PM
best way to get the nack is to start on simple items, Keep us posted with the progress on the manifold

#108
Posted 30 March 2008 - 02:18 PM
Also how much did it set you back from COME?
#109
_greenmachine215_
Posted 30 March 2008 - 02:43 PM

#110
_Viper_
Posted 02 April 2008 - 06:42 PM

I know its not a perfect intake manifold as it has square internal edges which isnt the best performance wise... But lets face it this isnt a top level drag car and the tiny ammount of Horsepower id lose wont be noticed... and Well I got it at a good price

But made a start on polishing it today, most of it is pretty flat so should be pretty quick and easy to do, bar the bottom half eep dreading that bit...
Before:
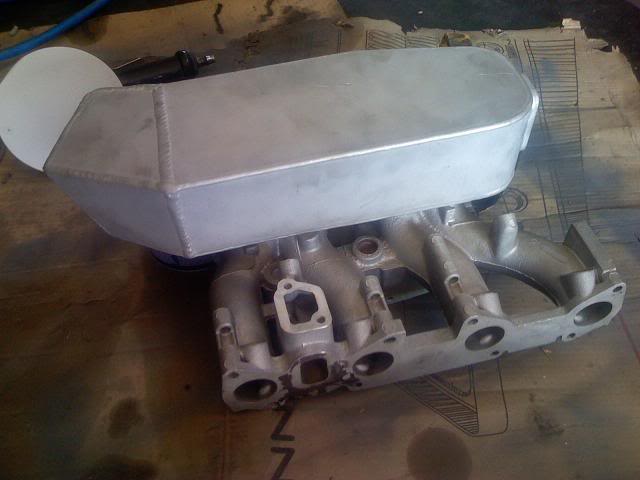
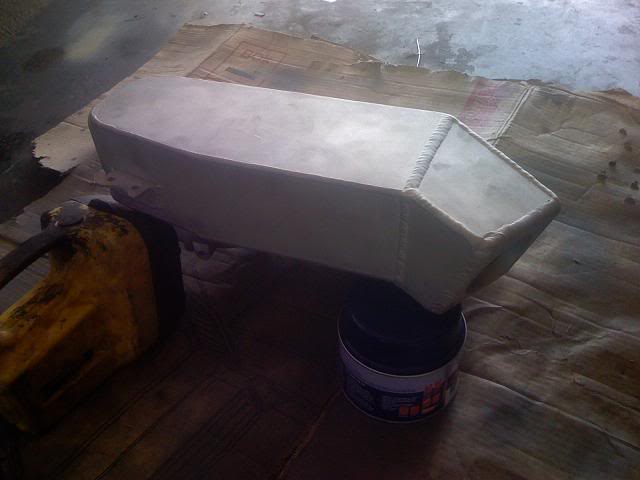
After 1/2 n Hour:

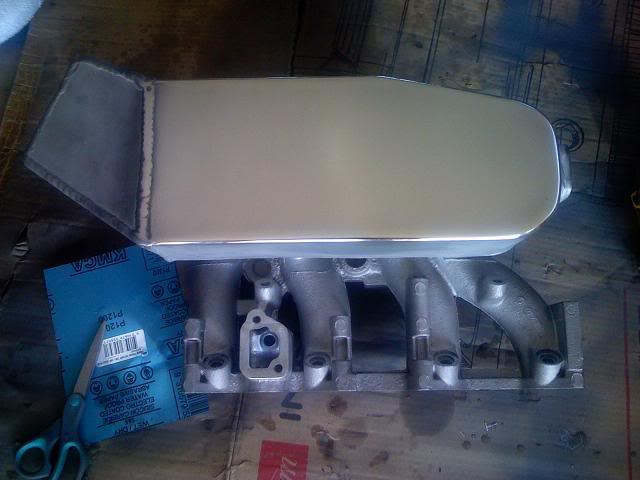
I only had sandpaper and some meguirs metal polish So could only get that hazzy sorta shine out of it...
there is about 3-4 spots on the top that are like chips (casting flaws?) and are about 1/2mm-1mm deep... Am I best to just ignore them? Or should I keep sanding and sanding and sanding till there gone?
I went 240 then 340 on the orbital sander, then 600, 800 dry with just a rubbing block then 1200wet then polish....
What do you guys recommend I do to get a mirror finish? Just get some of those Jasco blocks from bunnings and use the brown then white, then some Purple polish? or do some more sanding first?
Cheers

#111
_j7723_
Posted 03 April 2008 - 01:21 PM
Viper If I were doing that one I would go to the white with a soft wheel then purpleIthere is about 3-4 spots on the top that are like chips (casting flaws?) and are about 1/2mm-1mm deep... Am I best to just ignore them? Or should I keep sanding and sanding and sanding till there gone?
I went 240 then 340 on the orbital sander, then 600, 800 dry with just a rubbing block then 1200wet then polish....
What do you guys recommend I do to get a mirror finish? Just get some of those Jasco blocks from bunnings and use the brown then white, then some Purple polish? or do some more sanding first?
Cheers
Top job so far
#112
_Viper_
Posted 03 April 2008 - 09:22 PM

BUT, spent another hour on it tonight, just working on the huge welds this time and got them down level, which has left with with a couple of questions... Pics first

Before:
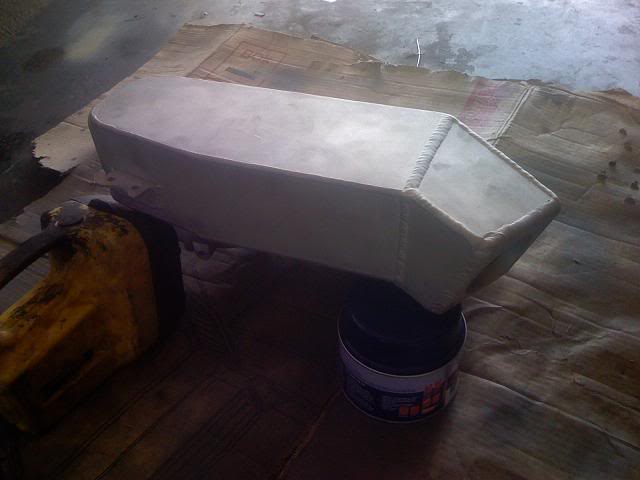
After:
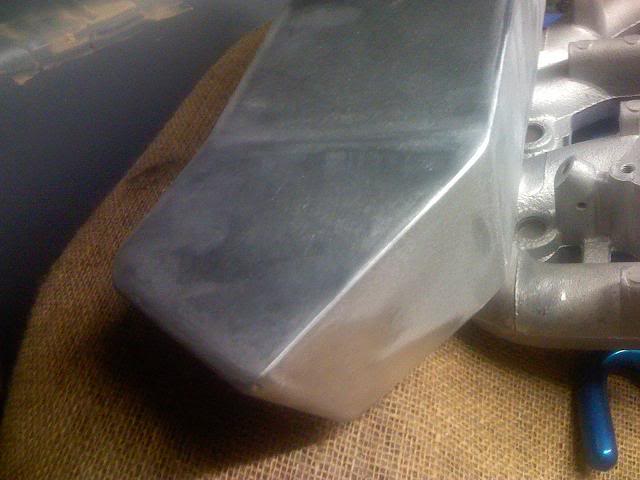
Ok questions time... anyone got any tips with working on rounded surfaces? and keeping it all even and nicely uh rounded?


Also found a couple of spots like this:
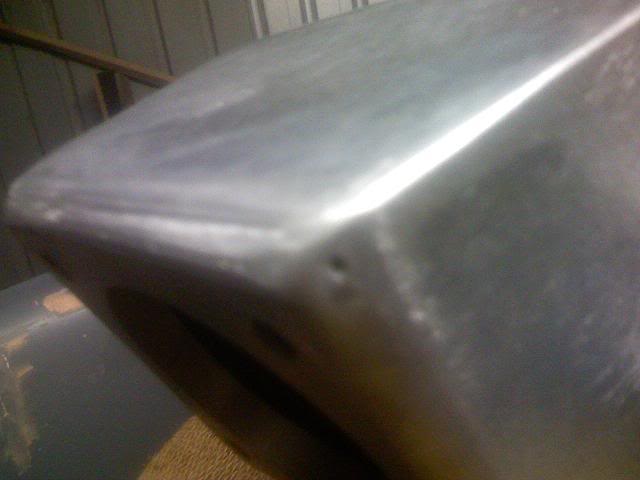
Not the best pic but you can see its a fairly deep hole in the weld. Now I could possible sand it down but would need to remove alot of material... Would it be best to find someone who can weld alloy to just weld the hole up and I grind it back down flat?
Cheers fellas

1.5 Hours work so far...
#113
_greenmachine215_
Posted 03 April 2008 - 10:16 PM
Tip: Get yourself one of them rubber sanding blocks from bunnings, put your paper in that and do your edges, this way you are sanding in an even pattern. where as by hand or rotary tool you tend to apply different pressure giving that ripple effect if you block sand the whole object i garuntee you will have an excellent ripple free finish.
I Know that imperfections and pours are a bitch, but look at it from a distance and you cant tell, if it was me id just put a touch of bog or something and cover the dot with a silver touch up pen, depends how hard you wanna go i guess,
Like how you smoothed out the tig welds One piece effect is awesome, cant wait to see it done and on the car
Are you doing the rest of the manifold runners?

#114
_Viper_
Posted 03 April 2008 - 10:24 PM
Rubber sanding block best hey? Ive got one of those medium density foam ones...
Yea should look sweet once its all done and cant see any welds

Hah umm still undecided about the lower half... would be ALOT more work... I was going to see if its possible to just get the lower half ceramic coated? or if they can only do a whole object.... Cos as you can see is very tight in there and would pretty much all have to be done with my pinky finger and not looking forward to that haha
#115
_greenmachine215_
Posted 03 April 2008 - 10:51 PM
It may seem like a shit load of work but if you have time and patience, It is the most rewarding thing when you stand back and look at the final product,
Good luck with it

#116
_Viper_
Posted 03 April 2008 - 11:50 PM
#117
_Viper_
Posted 06 April 2008 - 09:11 PM
But here's where its at now anyway

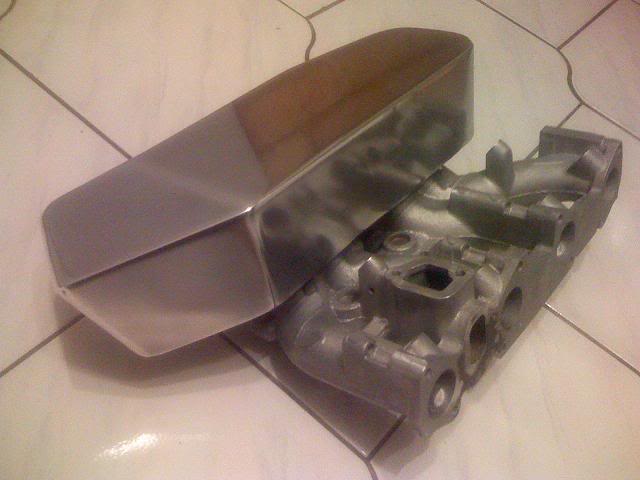
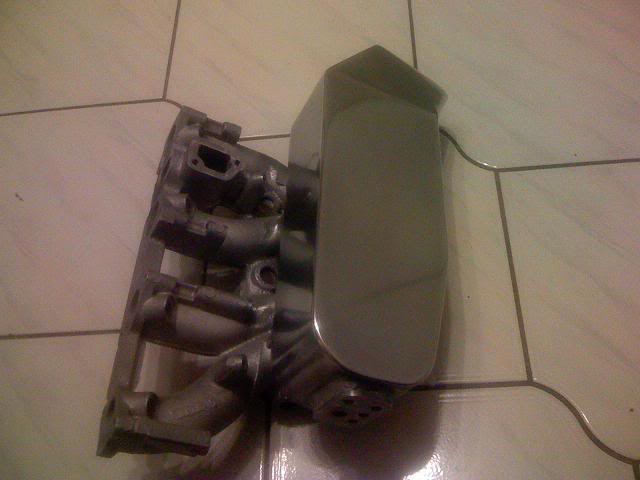
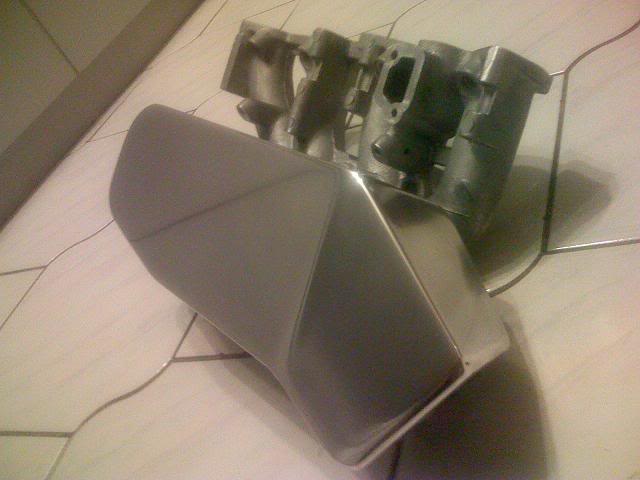
When your doin the very final polish ie with purple polish etc... whats the best thing to rub the purple in with? and is it best to rub it in by hand and push as hard and fast as u can.... or as slow and soft.. or fast and soft?
Then whats the best thing to give the final rub down? and yea hard n fast etc...
#118
_greenmachine215_
Posted 06 April 2008 - 09:27 PM

I always use flannelette bed sheets (the ones for winter) They are very soft and semi fluffy, no grain in the material,
Always work in a circular, figure 8 pattern be it sanding or polishing, This way you get an even finish and when the light angle hits there arent any Directional lines, With sanding you also get even finish No high/low spots.
thats the ways i do it, But if anyone else has tips that work lets hear it.
cheers
marc

#119
_Bomber Watson_
Posted 06 April 2008 - 09:32 PM

Just buy a box of babies nappies, the reusable ones. Then when they get dirty throw them in the washing machine.
Cheers.
#120
_jake_
Posted 06 April 2008 - 10:08 PM

#121
_Viper_
Posted 06 April 2008 - 11:52 PM
I jus used some autosol I had, will the purple polish fix this? or should I attack it more with the white compound? or is that the best u can expect...
oh yea and the welds all came up hell shiny, like 100% mirror finish, is this jus cos different alloys shine more or wha?
#122
_Herne_
Posted 07 April 2008 - 07:24 AM
Cheers
Herne
#123
_Viper_
Posted 07 April 2008 - 07:11 PM
Would it be better to use it in the drill due to the lower RPM (thats what I have used so far) or in the die grinder at high rpm?
#124
_Herne_
Posted 07 April 2008 - 07:33 PM
For smaller or tricky jobs such as bolt heads etc I use a flexible connection on a Dremel type tool also run at high speed.
Herne
#125
_Viper_
Posted 18 April 2008 - 12:05 AM


Here how it was originally:
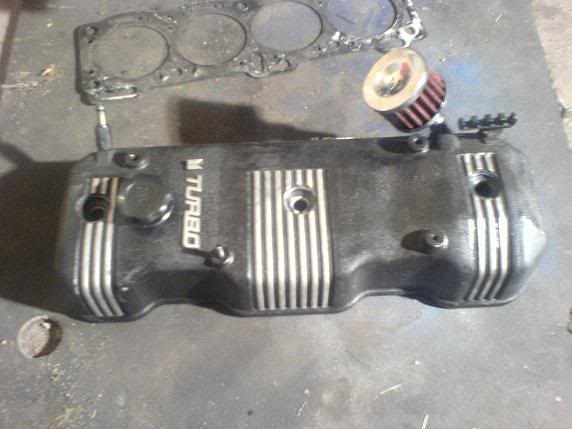
Bout half way:
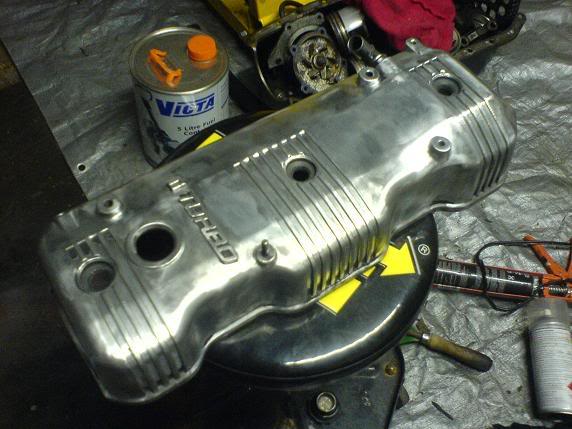
And as it is atm:
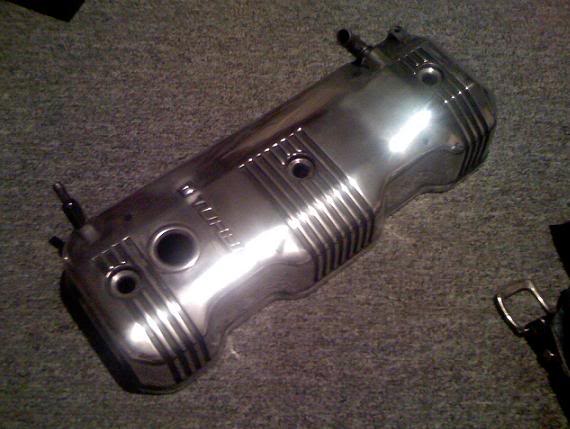
I tried to use just the white compound on the soft wheel straight away, but didnt come up with a mirror shine and can see very very slight scratches.... gonna have another go with grey and rougher buff, then the white again... Aiming for the full on mirror finish

Thanks for the tips guys, im getting there..
1 user(s) are reading this topic
0 members, 1 guests, 0 anonymous users