Ive been thinking of ways to strenghten up the chassis of my hatch, Im putting in an injected 6.3L so that means mountains of tourqe which means twisting chassis
I have thought of purchasing a chassis bolt on kit from castlemaine rod shop,
But also have seen a few forum members doing the chassis rail extension mod,
I just want to know if anyone knows the legallity's of this, It means chopping out some floor pan to fit the extension, would this be something that an engineer would need to do for it to be legal on the street, Because its not something you can just change back for roadworthy,
Heres a couple of pics i stole from 355LX.
Any information would be appreciated
Cheers

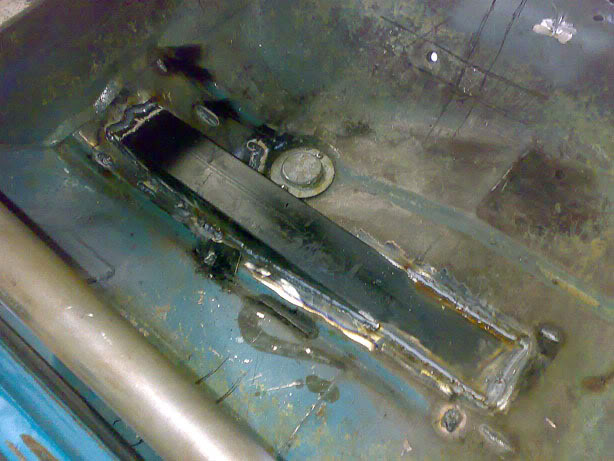
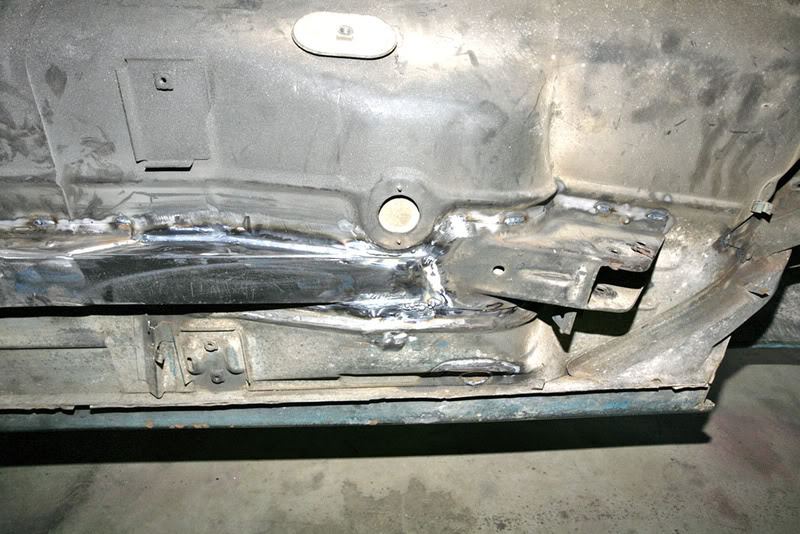