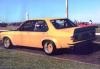
I'll show you how I cut guards from start to finish
#26
_Viper_
Posted 17 August 2008 - 10:17 PM
#27
Posted 17 August 2008 - 11:11 PM


#28
Posted 18 August 2008 - 09:07 AM
#29
Posted 18 August 2008 - 09:29 AM




Mort
#30
Posted 18 August 2008 - 09:47 AM
#31
Posted 18 August 2008 - 09:48 AM
1) fit a rear spoiler
2) reposition the bonnet scoop
3) cut the front edge of the flare and spoiler
4) some minor rust repairs
I have a good mate of mine who will be doing the touch up paint on this car so I 'll be taking a few pics of the car in the booth. As stated I am doing 4 cars so there will be plenty of stories and pics to follow. The 4 cars I am building are:
1) Allan Grice L34 replica
2) restore an original SLR5000
3) an A9X replica
4) repaint my fathers SLR5000
Ruts
#32
_LH350_
Posted 18 August 2008 - 01:07 PM
very informative. Its great to see someone take such pride in their work. Looking forward to seeing the finished product ;-)
#33
Posted 18 August 2008 - 01:53 PM
#34
Posted 18 August 2008 - 07:04 PM
i need to get my ass into gear and make a template for the rear quarters to fill the gaps i might wait to see the pics before i do anything
#35
_Yella SLuR_
Posted 18 August 2008 - 07:10 PM
More people should do these sorts of articles, it is very rewarding for everybody, including the person doing the work, as your work is under scrutiny (EDIT: as well as your angle grinder

Edited by Yella SLuR, 18 August 2008 - 07:11 PM.
#36
Posted 18 August 2008 - 07:25 PM
#37
Posted 18 August 2008 - 08:06 PM
Ok, today I put the infill in the 1/4 panel and finished off all the welds. Here is a picture of the 1/4 panel looking up from underneath. This shot shows the gap that we have between the inner wheel arch and the outer 1/4 panel.
cutting guards 089.jpg 113.12K
8 downloads
Now I know that a lot of people like to cut the outer 1/4 and then cut the inner wheel arch a bit longer and then fold the inner up so that it meets the 1/4 panel. Now there is nothing wrong with that method and done right it look good and does not leave any sharp edges for the wheel to hit, I have done it this way many times before and I encourage that method (I'll show you how I do it on my next build). The problem I have with this car is that there is not enough of the inner metal left to fold out and meet the 1/4 panel. This was because of the previous repair. So what do we do you ask, we make a filler piece out of steel to fit in the gap. But what needs to done first is to clean up the opening so that the filler piece fits snug. I do this by using a hammer and dolly.
cutting guards 088.jpg 263.51K
8 downloads
With a little bit of work the opening will allow a nice piece to put in. I actually had to open the gap up a bit so that the strip can be put in. When you cut the 1/4 open you will see that there is a double layer of metal in the inner wheel arch and what I like to do is to weld the gap closed first. Here is a picture of the cleaned up opening showing the second panel with a small gap exposed.
cutting guards 089.jpg 113.12K
7 downloads
I clamp the two panels together and weld them up with an oxy,
cutting guards 090.jpg 193.96K
7 downloads
cutting guards 091.jpg 286.57K
8 downloads
cutting guards 093.jpg 120.77K
7 downloads
When finished you should have a nice clean weld that looks like this.
cutting guards 094.jpg 174.3K
7 downloads
If your wondering whay I used the oxy it was because when I did my apprenticeship back in 1980 I only ever used an oxy and I can sometimes get a better weld with it. The only problem is the heat that it puts out which can distort panels very easily. A problem I had with this car is that it has about 30,000 coats of paint on it and when the paint burns it burns BIG.
Ok, now we have a nice clean opening it times to make template so that we can make a filler piece. I used a cardboard back cover off an exercise book.
cutting guards 095.jpg 125.34K
7 downloads
I then held the cardboard in place and then I got a hammer and tapped around the edges which should leave an outline on the cardboard matching the opening.
cutting guards 096.jpg 134.72K
9 downloads
I then cut the cardboard out on the marking that was left on the template and then laid the template on a sheet of metal, I use and old Dexion steel shelf as it is thicker than most panel steel. I then traced around the template with a texta and then cut the metal piece out.
cutting guards 097.jpg 168.65K
7 downloads
cutting guards 098.jpg 95K
7 downloads
cutting guards 099.jpg 152.45K
7 downloads
cutting guards 100.jpg 122.31K
7 downloads
I then put the filler piece into place and started tacking, remember slow and steady. Don't get too much heat in the 1/4 or you will distort the panel.
cutting guards 101.jpg 94.51K
7 downloads
cutting guards 102.jpg 117.98K
7 downloads
Once the filler piece is in place weld up all your gaps (BIT BY BIT). When done it should all look like this.
cutting guards 103.jpg 346.71K
9 downloads
cutting guards 104.jpg 208.15K
7 downloads
cutting guards 105.jpg 217.69K
7 downloads
cutting guards 106.jpg 223.24K
7 downloads
Attached Files
#38
Posted 18 August 2008 - 08:11 PM
#39
Posted 18 August 2008 - 08:31 PM
Once all the welding is done it's time to clean things up a bit. To do this I use my Rupes sander fitted with a velcro pad with 40 grit attcahed. This photo was taken after the job was done hence the stuffed edge.
cutting guards 107.jpg 131.89K
7 downloads
It should look like this when finished. Again be careful as the grinding disc can catch a sharp edge.
cutting guards 108.jpg 182.53K
8 downloads
cutting guards 109.jpg 212.31K
7 downloads
To clean up the edge on the dog leg I use a grinder and then finish the job by hand with a file. I do this as it gives me more control so that I don't take too much material off.
cutting guards 110.jpg 141.81K
7 downloads
Just when you thinks you've finished you find that you may have a couple of low spots in the weld that may need more welding so that you can clean up the weld with the file. I am pointing to a low spot that needs more weld so that I can file a nice smooth edge in the dog leg.
cutting guards 111.jpg 111.69K
8 downloads
cutting guards 112.jpg 175.51K
7 downloads
cutting guards 113.jpg 165.21K
7 downloads
Once welded I again attack it with a file to get a nice clean edge now with no low spot.
cutting guards 114.jpg 180K
7 downloads
Who says no-one does metal finishing anymore.
cutting guards 115.jpg 152.45K
7 downloads
When I finished the 1/4 I went back and finished the welding on the door. When the welding was done I cleaned up the door edge with a small belt sander, which we in the panel game call a 'Sticky Beek' (however I'm not in the panel game anymore)
cutting guards 116.jpg 29.97K
7 downloads
cutting guards 117.jpg 103.15K
7 downloads
cutting guards 118.jpg 156.83K
7 downloads
cutting guards 119.jpg 104.53K
7 downloads
When it's all done the opening should look something like this.
cutting guards 121.jpg 132.23K
7 downloads
Well that's it for today. I have to go to Sydney tomorrow but I may do some more in the afternoon. Next step is to refit the flare and then make a couple of small metal tabs to help hold the flare in place just like the A9X's had (or am I wrong Red) as well we might have to do a bit of glass work on the flares themselves. The way that I put the piece between the 1/4 and the inner guard gives us a flat surface just in case the body comes down that far and hits the wheel, no sharp edges. If you look at it and think 'gee that finish looks ugly', don't panic there's a bit to go yet.
STAY TUNED
Ruts.
#40
Posted 18 August 2008 - 08:34 PM
#41
Posted 18 August 2008 - 08:41 PM
mark
#42
_Yella SLuR_
Posted 18 August 2008 - 10:29 PM
#43
_SS Hatchback_
Posted 18 August 2008 - 11:12 PM
#44
Posted 19 August 2008 - 08:21 AM
Ruts
#45
_Rob 5000_
Posted 19 August 2008 - 07:34 PM

#46
Posted 19 August 2008 - 07:51 PM
Ruts
#47
Posted 20 August 2008 - 08:39 AM

Mort
#48
_rorym_
Posted 20 August 2008 - 05:25 PM


R
Edited by rorym, 20 August 2008 - 05:26 PM.
#49
_Yella SLuR_
Posted 20 August 2008 - 07:35 PM
#50
Posted 20 August 2008 - 08:25 PM
Hello one and all. Well it has been a productive day in the shed and as such here I am again downloading pictures and typing a story for all to read.
Before we get into things I want to just tell everyone that whilst working on this car today it revealed that it has had some extensive bodywork done in the past. When you read this article I ask that everyone keep the comments about the previous repairs to themselves. In short I'll say it all now, this car has plenty of body filler in the doors and 1/4 panel but saying that I have not found any of it wanting to fall out in that the filler had sweated resulting in rust forming between the filler and the panel. Done correctly body filler will last for years and even thought this car has some in it it seems to be done right however a bit less would suit me. Remember this car belongs to a fellow member.
Ok, when I sat back and had a good look at the opening left in the wheel arch I noticed that there was a piece sticking out towards the rear of the arch and I was thinking that this bit could cause tyre damage if a big pot hole was struck. In the back of my mind I was never happy about leaving this bit as it was. You can see what I'm talking about as I have drawn an arrow pointing to the area. I have put the wheel back on and you can see that it is near the tyre.
cutting guards 122.jpg 165.34K
9 downloads
So I took to this bit with the grinder and cutting wheel and took a bit more off.
cutting guards 123.jpg 162.41K
7 downloads
Nothing sticking out to hit the wheel now.
cutting guards 124.jpg 162.14K
8 downloads
I then welded up the edge and tidied things up a bit with a hammer and dolly.
cutting guards 125.jpg 147.47K
7 downloads
I'm happier now with the way it looks. When you look up underneath the flare covers the rear of the wheel arch and when the flare is back on it's look a lot better.
cutting guards 152.jpg 195.25K
7 downloads
Now that I was happy with the wheel arch it was time to weld the holes up in door and 1/4 panel that are not covered by the re positioning of the flares. I have marked the holes that need filling.
cutting guards 127.jpg 156.11K
9 downloads
I noticed that when I looked down from above you could see that the holes were actually protruding from the door and needed a bit of work to make them smooth before welding. This shot is from above looking down showing the door skin protruding around the hole.
cutting guards 128.jpg 116.11K
7 downloads
I used a hammer and dolly to straighten things up a bit.
cutting guards 130.jpg 229.33K
7 downloads
cutting guards 129.jpg 112.16K
7 downloads
When I was happy with the door skin I used another of my hand grinders to take off the paint around the holes.
cutting guards 132.jpg 146.85K
7 downloads
cutting guards 133.jpg 182.61K
7 downloads
cutting guards 135.jpg 128.11K
7 downloads
As the holes in the doors and 1/4's were a fair size I had two options. Either make a number of small patch panels and put them in the holes and well them up or take another of my trusty tools and fill the holes with weld. What I do is get a piece of brass, either a big tap fitting or an air connection. I used both today.
cutting guards 134.jpg 98.14K
8 downloads
cutting guards 144.jpg 82.31K
7 downloads
What you do is take whatever you use as long as it is made of brass and place it behind the hole. What happens is is that you can still weld the hold as the brass tool still allows and arch but stops the weld falling inside the hole which can cause the welder to blow the edge away from the hole creating an even large hole and more work. When you have finished just take the brass tool out as weld does not stick to it. It's an old trick but very effective. Remember to turn the amps down on the welder so that it does not burn so hot. Here is the brass tool inside the door and 1/4. It's a much harder job when working by yourself (I'll have to get me some friends).
The door
cutting guards 140.jpg 125.15K
8 downloads
The 1/4
cutting guards 146.jpg 168.23K
6 downloads
When I start welding I take my time and jump from hole to hole doing a bit of each of the holes at a time. As I weld I use an air blower and cool the weld off to help stop panel distortion.
cutting guards 138.jpg 109.48K
6 downloads
cutting guards 139.jpg 156.08K
6 downloads
cutting guards 143.jpg 107.77K
7 downloads
cutting guards 142.jpg 134.7K
9 downloads
cutting guards 141.jpg 160.57K
7 downloads
Once all the welding is done where ready to smooth the welds off.
cutting guards 148.jpg 163.94K
7 downloads
I'll close this bit to keep some happy. More to follow.
1 user(s) are reading this topic
0 members, 1 guests, 0 anonymous users