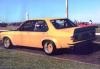
I'll show you how I cut guards from start to finish
#51
_Rob 5000_
Posted 20 August 2008 - 08:47 PM
#52
Posted 20 August 2008 - 09:25 PM
Ok so we have closed the first bit so that Yella can have a read so here we go with the next.
Once all the holes are welded up and I'm happy with it I smooth the welds with my hand grinder with a stone wheel. Do not grind the welds completely flat. I finish the welds off with my other grinder with the paper disc attached. This one leaves a nice smooth finish.
Stone wheel
cutting guards 149.jpg 155.81K
8 downloads
And finish with this one.
cutting guards 132.jpg 146.85K
7 downloads
When done it should all look like this.
cutting guards 150.jpg 160.42K
7 downloads
I then refitted the flares and it looked like this.
cutting guards 151.jpg 108.52K
7 downloads
Ok I suppose I could say that that's all the guard cutting and welding done but I said at the start that I would see thing through right to paint. In regards to the cutting process what I have decided to do is to cut the driver's side different to the one we have just done. On the driver's side I'll do the old 'cut and fold' technique but more on that another time.
What I am going to do now is keep going with the drivers side and show you how I add small pieces of metal to the door flare and 1/4 panel that help hold the flares in place to give a nice even gap. So let's have a look at the passenger's door flare. When the flare was first put on the door I had to hold the flare against the door before I put a self tapper in it to hold it against the door, remember this
cutting guards 032.jpg 109.55K
6 downloads
cutting guards 033.jpg 126.45K
6 downloads
cutting guards 154.jpg 95.58K
6 downloads
cutting guards 153.jpg 118.81K
6 downloads
So what we want to do is find a way of holding the flare against the door with no screws showing from the inside. What I do is make a small metal tab and fiberglass it to the inside of the flare so that I can use a screw or pop rivet from the inside to hold the flare in place.
cutting guards 156.jpg 92.85K
6 downloads
When your happy with your small metal tab clean the inside of the flare so that the new glass will stick. I used my 'sticky beek' belt sander for this.
cutting guards 158.jpg 130.72K
7 downloads
cutting guards 159.jpg 93K
6 downloads
I then get my fiberglass repair kit and glass the small metal tab to inside the flare. This gives me something solid to screw to pull the flare to the door.
cutting guards 157.jpg 173.28K
6 downloads
cutting guards 160.jpg 139.6K
6 downloads
cutting guards 161.jpg 93.31K
7 downloads
Well that's it for now I'll show you how I attach it to the door when the glass dries and then we'll make the metal tab to hold the 1/4 panel flare in place to match the door. I'm back at work tomorrow but I should get to the shed in the afternoon to at least fit the door flare so,
SEE YOU THEN.
Ruts
#53
_Yella SLuR_
Posted 20 August 2008 - 10:16 PM
#54
Posted 21 August 2008 - 10:06 AM
ask a sparky for a bus bar from a transformer or similar.
Edited by arrimar, 21 August 2008 - 10:07 AM.
#55
Posted 21 August 2008 - 12:57 PM

Grant..
#56
_Yella SLuR_
Posted 21 August 2008 - 11:45 PM
#57
Posted 30 August 2008 - 08:08 PM
G'day all, sorry for the delay I've been a tad busy at work which makes me a bit tired when I get home so the shed is the last place on my mind. Plus the fact that I have built a pergola in the last couple of days. The things we do to keep the boss happy.
Anyway when I last left I had just glassed a small metal tab in behind the door flare. Why do I do this you ask, well it is to hold the flare against the door with a small screw from the inside.
Remember this:
cutting guards 033.jpg 126.45K
8 downloads
When we put the small tab on the inside we can screw the flare from the inside so that we can glass the hole on the outside. Here is the flare fitted with the screw in place.
cutting guards 162.jpg 98.57K
8 downloads
Well that's about it for the flare on the rear door so we'll do some work on the 1/4 panel flare where it meets the door. What you need to do is make a small metal tab just like the one on the door flare. I used a small bracket and cut it up to suit.
cutting guards 164.jpg 93.94K
7 downloads
I then welded the small 90 degree angle onto the 1/4 behind the flare. What this does is it allows you to put a small screw or pop rivet through the flare and into the bracket to hold the flare out and into place.
cutting guards 165.jpg 159.54K
8 downloads
cutting guards 168.jpg 181.77K
6 downloads
cutting guards 169.jpg 197.28K
6 downloads
Unfortunately that's as far as I got with the rear of the car today as I thought that I would attack the front to give the front wheel more clearance on full lock. Don't worry I'll get back to the rears in a few days.
Ok, here we go with a very quick adjustment on the front. This job took me about an hour to do. What most people do in this case is just take to it with a ball pein hammer and bash it into place as someone had done previously.
Remember this
cutting guards 017.jpg 152.9K
6 downloads
cutting guards 024.jpg 178.58K
9 downloads
What happens in this case is that when you bend over the metal in this area it just folds the lips but still leaves material that can still hit the wheel. To get ample clearance with just a hammer one would need to bash the crap out of this area. What I like to do is take to with cutting wheel and slice through this area, move everything back and then re-weld it all up again.
First I make my cuts and remove some metal
cutting guards 171.jpg 318.98K
9 downloads
cutting guards 170.jpg 311.94K
7 downloads
I use some heat to move the area back
cutting guards 172.jpg 262K
7 downloads
cutting guards 173.jpg 333K
6 downloads
I then fold the outer lip over the area that I just heated and moved back
cutting guards 174.jpg 145.01K
7 downloads
I then weld the outer to the inner
cutting guards 177.jpg 275.86K
7 downloads
Just be careful of fire when your welding if working by yourself. If I'm working alone I put a wet rag on the inside. If you have a friend just get them to watch on the inside and be ready with a bucket of water and wet rag.
cutting guards 179.jpg 175.47K
6 downloads
When finished inside looks like this
cutting guards 180.jpg 173.12K
6 downloads
I then cover with Sikerflex and under body sealer.
cutting guards 183.jpg 199.16K
6 downloads
I then also spray the area under the guard with body sealer like when it left the factory
cutting guards 181.jpg 238.12K
6 downloads
cutting guards 182.jpg 199.11K
6 downloads
With the wheel back on we now have ample clearance for big wheels and full lock all in about an hour. You can't see it in these pictures but I can get my fingers in behind the wheel on full lock.
cutting guards 178.jpg 121.05K
9 downloads
cutting guards 192.jpg 171.72K
6 downloads
Stay tuned for the final flare fitting chapter (say that three times fast) in the next few days.
Ruts.
#58
_SS Hatchback_
Posted 30 August 2008 - 08:39 PM
#59
_Marshall_
Posted 30 August 2008 - 09:34 PM
If you want to do a "How to fit flaires to a Hatch"
I'll donate my hatch, flares / spoiler etc, and $$$'s to the cause

#60
Posted 31 August 2008 - 09:52 AM
#61
_Marshall_
Posted 31 August 2008 - 10:05 AM
I'll keep it in mind if I get some free time. Where are you situated.
Melbourne (Alphington)
#62
_SS Hatchback_
Posted 31 August 2008 - 05:11 PM
#63
_project LH_
Posted 28 September 2008 - 10:53 AM
#64
Posted 15 November 2008 - 09:34 PM
Well it's been a bit of time between drinks but I've been on leave for 4 weeks and the wife has had me doing all the normal jobs around the house that one does while on holidays, (plus I did a couple of weeks of lying on the lounge just doing nothing which has been a bit of a change).
So here we go again, after finishing all the welds and grinding on the passengers side rear flair I finished all the repair work and it is finally ready for paint except for a little work on the flair itself,
cutting guards 033.jpg 126.45K
8 downloads
cutting guards 034.jpg 159.63K
7 downloads
cutting guards 035.jpg 161.8K
7 downloads
after finishing this side I moved onto refitting the bonnet scoop that someone had put on earlier in the wrong position, remember this
cutting guards 018.jpg 193.22K
9 downloads
To try and save the owner the price of new bonnet I decided to move the scoop into the correct position and then weld the exposed holes up and finish the spot welds, seems all worked out.
spoiler flares 030.jpg 145.81K
8 downloads
spoiler flares 030.jpg 145.81K
8 downloads
spoiler flares 031.jpg 188.31K
7 downloads
spoiler flares 032.jpg 208.27K
8 downloads
After finishing the bonnet mods I decided to refit the passengers front flair. After cutting the lip off the guard you will find that it will make the guard weak and flimsy so what you need to do is make a new lip to give the guard its strength back. What I did is take a pair pliers and bend a small flair back on the guard,
spoiler flares 001.jpg 124.04K
7 downloads
spoiler flares 002.jpg 117.85K
8 downloads
After doing this I re-positioned the flair so that its site in the correct spot. Have a look at the old holes and see the difference between the old (large hole) and new (small hole).
spoiler flares 008.jpg 104.83K
7 downloads
Once I sat the flair back on I had to realign the front spoiler and then modify it so that it would clear the front wheel on full lock. This cars front flair were already cut so I had to do this modification different to the way I normally do but I think it will still look good in the end.
spoiler flares 009.jpg 138.98K
7 downloads
When I was happy with how much I was going to take off I cut the flair and spoiler and then reshaped it with the grinder to give it a more even look. I'm happy with the way it turned out.
spoiler flares 010.jpg 144.18K
8 downloads
spoiler flares 011.jpg 152.12K
7 downloads
spoiler flares 012.jpg 187.57K
7 downloads
Ok after the passengers front was finished I started on the drivers rear,
spoiler flares 013.jpg 134.46K
7 downloads
To make things easy all I did was use the bits that I cut out on the passengers side and trace around them to give me the same cuts.
spoiler flares 014.jpg 102.6K
7 downloads
spoiler flares 015.jpg 163.08K
7 downloads
spoiler flares 016.jpg 136.88K
7 downloads
spoiler flares 017.jpg 145.1K
7 downloads
After the cuts were made I cleaned the edges up with the disk grinder and we're ready to weld tomorrow.
spoiler flares 020.jpg 177.84K
7 downloads
Here's a picture of the two door pieces side by side
spoiler flares 019.jpg 234.36K
7 downloads
#65
Posted 15 November 2008 - 10:02 PM
Ok, while in the typing mode I thought I would show you a quick rear spoiler repair I did to try and save the owner the price of new one. When the car was dropped off the owner gave me a spoiler to fit on the rear. I noticed that it had no mounting bolts so I was wondering what to do to mount it. This is what it originally looked like with no mounting screws or bolts.
rotisserie 001.jpg 381.43K
7 downloads
rotisserie 002.jpg 311.63K
7 downloads
rotisserie 003.jpg 392.37K
7 downloads
rotisserie 004.jpg 418.33K
7 downloads
rotisserie 005.jpg 313.63K
7 downloads
rotisserie 006.jpg 248.2K
7 downloads
Ok, so what I did was make some mounting plates and welded small nuts to the plates and then fiberglass the plates with the nuts attached to the rear lip of the spoiler where it meets the rear of the boot lid.
spoiler flares 023.jpg 130.29K
7 downloads
spoiler flares 022.jpg 111.11K
6 downloads
I then cut some small plates and welded two bolts to them and then glassed the plates and bolts to the spoiler. When I measured where the holes need to be I drilled the boot lid and found that it sat very well on the boot lid.
spoiler flares 021.jpg 169.83K
7 downloads
spoiler flares 027.jpg 121.31K
6 downloads
spoiler flares 026.jpg 137.89K
6 downloads
spoiler flares 028.jpg 106.63K
6 downloads
When I was happy with the fit I glassed the old holes that were left in the spoiler. A little finish off and its ready for paint.
Stay tuned.
spoiler flares 025.jpg 137.78K
6 downloads
spoiler flares 024.jpg 129.75K
6 downloads
#66
_LH350_
Posted 16 November 2008 - 01:56 PM
#67
Posted 16 November 2008 - 09:13 PM
#68
Posted 16 November 2008 - 09:51 PM
#69
Posted 16 November 2008 - 10:45 PM
#70
Posted 16 November 2008 - 10:54 PM
As much as I don't like flares, I can definitely appreciate the amount of work that goes into a quality fit-up... All too often they are fitted badly, with shocking gaps etc, which I think is why I'm not a fan. Good work though, good to see someone doing it right

Tim
#71
Posted 17 November 2008 - 11:10 PM
Ok, I had a pretty productive day as I got the drivers side rear all welded up. Now I'm always looking for a better way to do things and I very rarely do the same thing twice exactly the same way. So what I did was sit and stared at the wheel arch opening for some time trying to come up with an easier and tidier way to do things. What I came up with was a way that I think makes the job a lot easier and if done correctly may not need any paint on the 1/4's. So here it is,
what i did was to cut the inner wheel arch longer than the outer 1/4 panel. You do this I you want to do the old bend the inner around and meet the outer and then weld the two together. We're not going to do it that way. So cut the inner longer that the outer,
drivers flares 001.jpg 149.51K
9 downloads
drivers flares 002.jpg 87.66K
7 downloads
What you do then is go to the local hardware store and get yourself some 20ml x 3ml flat bar,
drivers flares 003.jpg 111.74K
8 downloads
When I cut it to the length of the arch I just began to bend it over my knee to try and match the shape of the opening, I even used the rear drum to bend the flat bar, and by the way it bends fairly easy so don't get heavy handed.
drivers flares 004.jpg 117.05K
7 downloads
drivers flares 007.jpg 267.58K
7 downloads
As you go just keep trying the bar in place to see if your getting close,
drivers flares 005.jpg 115.58K
8 downloads
By the time your finished it should fit pretty snug without pushing up with much pressure.
drivers flares 006.jpg 97.17K
9 downloads
When you have a snug fit you can tack the flat bar into place,
drivers flares 008.jpg 116.22K
6 downloads
drivers flares 009.jpg 143.2K
6 downloads
drivers flares 010.jpg 98.18K
6 downloads
I had to tap the inner skin to meet the flat bar as I went but it all fitted fairly well (to my surprise).
drivers flares 011.jpg 119.96K
6 downloads
I then began tacking the outer skin of the 1/4 to the flat bar. I then continued along at different intervals as you do not want to heat up the 1/4 panel too much or you will get panel distortion, remember to take your time or you'll pay for it later.
drivers flares 013.jpg 122.58K
7 downloads
drivers flares 014.jpg 101.14K
6 downloads
drivers flares 015.jpg 129.63K
6 downloads
drivers flares 016.jpg 112.77K
6 downloads
drivers flares 012.jpg 207.19K
6 downloads
drivers flares 017.jpg 121.01K
6 downloads
drivers flares 018.jpg 119.78K
6 downloads
When this section was finished I just finished welding the dog leg and the door the same way I did on the passengers side.
drivers flares 019.jpg 289.53K
10 downloads
drivers flares 020.jpg 129.53K
7 downloads
When it was all welded and ground down I was very happy with the finish. The flat bar on the 1/4 wheel arch went in so well that I will NOT have to paint anything above the flare line (what a bonus). Note how smooth the arch is front start to finish, very happy.
drivers flares 021.jpg 161.68K
7 downloads
drivers flares 022.jpg 127.83K
7 downloads
drivers flares 023.jpg 135.18K
7 downloads
drivers flares 024.jpg 131.72K
8 downloads
If your thinking to yourself this all seems too technical then just think of it as putting in a vary small wheel tub. Now you are probably thinking why would I want to do the wheel arch this way, well it's very simple. There is nothing worse than filling your petrol tank and then put three heavy people in the back only to find that when you drive down the road and hit a large bump that the wheel bottoms out on the inner wheel arch and slices or takes big chunks out of your tyres. By doing the wheel arch this way if and when the tyre bottoms out it will hit a flat spot and you may save your tyres, just a thought.
Attached Files
#72
Posted 17 November 2008 - 11:26 PM
So the wheel arch is in place and all welded. You will see that the flat bar sticks out past the 1/4 panel and I think that there is nothing wrong with this as its all up under the flare. But what you have to do is grind and small amount off the flat bar at the front where it meets the door so that the flare will sit in the correct position. If you don't grind this bit out the flare will stick up at funny angle,
drivers flares 025.jpg 101.21K
8 downloads
I then put the flares on the door and 1/4 panel and lined up the top at the flare halves but this is where I hit a problem. With the flares sitting the correct position the gap between the two was out. It was closer at the top than at the bottom. Now to get an even gap I had to take drastic measures and slice the flare and move the front flap forward until I got the gap I was happy with.
drivers flares 026.jpg 109.36K
9 downloads
drivers flares 027.jpg 108.43K
8 downloads
drivers flares 028.jpg 94.08K
9 downloads
Now what I have to do is glass the flare with the gap that I'm happy with but that's tomorrow SEE YA.
#73
Posted 19 November 2008 - 06:47 AM
Ok, as you can see by the last picture I made a vertical cut at the front of the flare where it meets the door so that I can fix the gap between the door and the flare. When I'm happy with the gap I grind the paint off the flare back to the raw fiberglass so that I can put some fibermat filler in the gap which will hold it in place until I can take the flare back off and strengthen it inside with resin and fiberglass mat. To old the flare in place while I mix some filler I use racing tap at the bottom edge of the flare,
drivers flares 029.jpg 113.49K
8 downloads
I then take my trusty bog mixing board (Torana 1/4 glass window)
drivers flares 030.jpg 206.22K
8 downloads
And mix the amount of fibermat filler I think I'll need
drivers flares 031.jpg 241.42K
7 downloads
And then put it in the gap and let it set
drivers flares 032.jpg 126.07K
8 downloads
While that was setting I finished the drivers side front flare exactly the same way as the passengers side. I then drilled all the holes in the small metal tabs that I welded under the flares and screwed the flares to the body. This does two things, firstly it holds the flare in place and secondly it adds strength to the flare when screwed to the body. If I had used the flares from Fibre Sports at Taren Point I could have grabbed the flares and rocked the car back and forth as the quality of the their product is second to none.
Drivers side rear door
drivers flares 033.jpg 95.38K
8 downloads
Passengers rear door
spoiler flares 005.jpg 128K
7 downloads
Drivers 1/4 panel
drivers flares 034.jpg 110.04K
7 downloads
Passengers 1/4 panel
drivers flares 036.jpg 120.19K
7 downloads
Well there's not much to do now to prep for paint so there will be only one more installment in regards to repairs so that I can show you the finished and primed product. I said that I will see this thing through to paint so,
STAY TUNED
Ruts
#74
Posted 19 November 2008 - 07:33 AM

Thats a really good idea, such a simple idea!
Great work mate!
#75
Posted 19 November 2008 - 10:44 AM

Won't be doing the cutting of the guards yet but the bit on lining up the flares to get the right gaps will come in very handy.
Can't wait for the paint and final finish.
Mort
1 user(s) are reading this topic
0 members, 1 guests, 0 anonymous users