
What Gauge metal to use
#1
_OZZ80Y_
Posted 29 June 2010 - 08:50 PM
If im hopeless theres no way i'll be touching the old girl but any help would be great.
Not trying to cut costs on my build but id feel more satisfied with myself if i know i can stand back and say, i built that.
Cheers, Mat
#2
Posted 29 June 2010 - 08:53 PM
Or you could just cut up an old door.
#3
Posted 29 June 2010 - 09:52 PM
Will work out easier and probably cheaper.
#4
_OZZ80Y_
Posted 29 June 2010 - 10:18 PM
the welder i have uses gas, its a toolex 140n, uses argon C02 gas. The misses old man works for boc so the gas on't be a problem.
Im from western sydney, anyone able to tell me where i can get some steel. Can i get it from bunnings.
Cheers
#5
_nial8r_
Posted 30 June 2010 - 07:37 AM


#6
Posted 30 June 2010 - 08:27 AM
Grab some different thickness material & try all of them.
Edited by Statler, 30 June 2010 - 08:28 AM.
#7
_freddy_
Posted 30 June 2010 - 01:00 PM
hope this helps matthew.
#8
_Bomber Watson_
Posted 30 June 2010 - 08:00 PM
Soooo much nicer with <3mm steel.
Cheers.
#9
_OZZ80Y_
Posted 30 June 2010 - 09:03 PM
The wire i already have on the welder is .8, how do you think that will go bomber?
I think the only replacement panels i will buy will be floor pans for each sides and lower sill for the pass side.
Well until i find more rust. there is so much high fill over the car.
#10
_freddy_
Posted 30 June 2010 - 09:45 PM
#11
_nial8r_
Posted 01 July 2010 - 08:33 AM

#12
_Bomber Watson_
Posted 01 July 2010 - 05:41 PM
The .6 is way better, but the .8 will do it.
Cheers.
#13
Posted 01 July 2010 - 06:04 PM

#14
_nial8r_
Posted 01 July 2010 - 08:52 PM

#15
Posted 02 July 2010 - 11:26 AM
Hope this helps cheers Dave
#16
_dirtbag_
Posted 18 July 2010 - 12:21 AM
As for steel, use zincaneal (spelling??). It's much more rust resilliant, stronger and around here anyway it's easier to find. Bright or black steel is good if you're making a roof skin or bootlid or something with an english wheel as it's softer. Anyway, any sheet will do : ) Yes, that's my weak excuse for a "sh1t" joke : )
When I do panel work, I use 1.2mm zinc, just so you know.
#17
Posted 18 July 2010 - 12:56 AM
#18
Posted 18 July 2010 - 07:14 PM
Cheers Dave
#19
Posted 24 January 2011 - 12:45 PM
Cheers
Max
#20
_Liam_
Posted 24 January 2011 - 05:25 PM
#21
_Yella SLuR_
Posted 24 January 2011 - 06:56 PM
Sheet metal supply: Offcuts from a steel/metal shop, they are the ones that also sell sheet, and most do a little in-house fabrication.
Practice: Start by playing with the settings and just weld some lines across the face, looking at speed, and penetration. Also settings, there are some settings on a mig Amps/wire feed that will not weld, you need to find the settings that work (nice sharp cracking sound)
Next try some spot welds butting pieces together. Lie the plates flat on something that can take heat (welding block) and slightly angle plates apart to allow for them pinching together as you spot them.
Next try seam weld the butt joint above.
Have fun.
I also have a TIG attachment for my stick welder. Can't do Ally, but gives a nice exact flame, and a bit more farking around, but I like it. Can weld anything of any thickness, and temperature control is great, but you have to sharpen the tungsten electrodes fairly regularly. Also different electrodes for different metals, but I mainly only do steel and stainless.
Edited by Yella SLuR, 24 January 2011 - 07:05 PM.
#22
_Yella SLuR_
Posted 24 January 2011 - 07:11 PM
Did a car restoration course at TAFE at night, and shite, part of it was oxy welding. Turned out when shown how I was quite good at it, so went and did a Welding and Thermal Cutting Course after that!!! That Car Restoration course was the best course I ever did. First part is a bit obscure (hub cap and wheel chock from sheet metal), but next bit is good (repairing chisel gashes to doors, patch panels to corners of doors, and panel preparation for paint).
You can do shite like this (was ready for the tip):
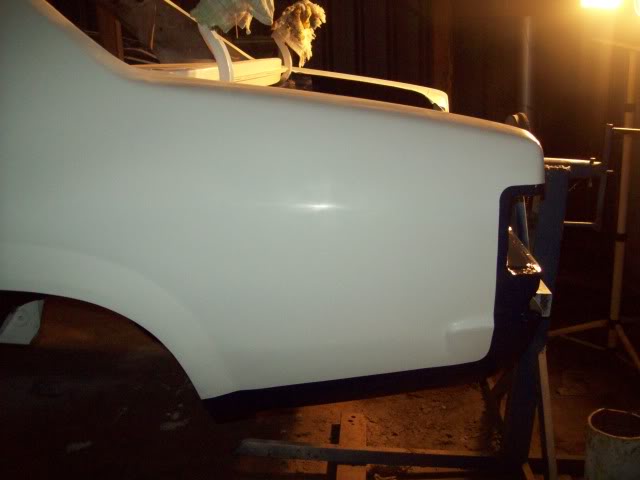
You'll also need some more tools: plenishing hammer, dolly, speedfile, bodyfile, mallet as starters.
Good luck with it.
Edited by Yella SLuR, 24 January 2011 - 07:21 PM.
#23
_TorYoda_
Posted 24 January 2011 - 10:08 PM
Edited by TorYoda, 24 January 2011 - 10:11 PM.
#24
Posted 24 January 2011 - 10:16 PM
#25
Posted 24 January 2011 - 10:22 PM
Oxy welding (or brazing) is your worst enemy on sheet steel car panels. Any form of flame welding burns the carbon from the steel leaving it as tin. Once the carbon is gone tin will rust at an extremely aggressive rate if it cannot be properly prepped and sealed on Both sides. TIG is not as bad as oxy, However if you can master the mig with .6mm wire you will get great results. After many years of experience I can butt weld panel steel with the mig using .6 wire in continuous runs...... I choose to do this to eliminate the overlap joint that holds moisture and assists the start of new rust. Practice with different settings, keep it clean and free of paint/zinc/gal etc and you will soon be getting satisfactory results.
This is dribble.
Oxy is the best if you are good at it.
Which I,unfortunately am not.
It is a dying craft which most metalworkers and panelbeaters no longer use due the time restraints and the skill and training involved.
Panelsteel composition has also changed,which renders it useless on modern vehicles.
1 user(s) are reading this topic
0 members, 1 guests, 0 anonymous users