Far out brussel sprouts
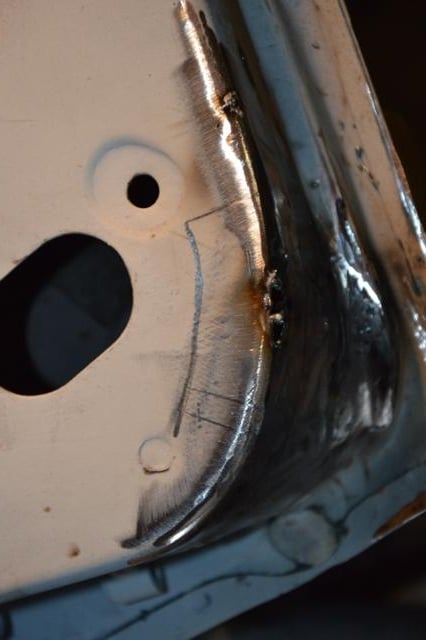
So marked it out, there is that overlaped bit in there someone so to be safe i went in a bit more. I did it 20mm from about 5 different spots and join the dots thinking it would be easier in the long run.
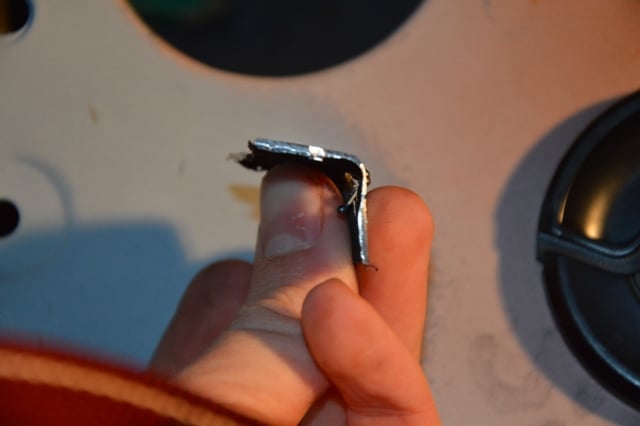
You can see how the bit right up the top is thinner some how.....
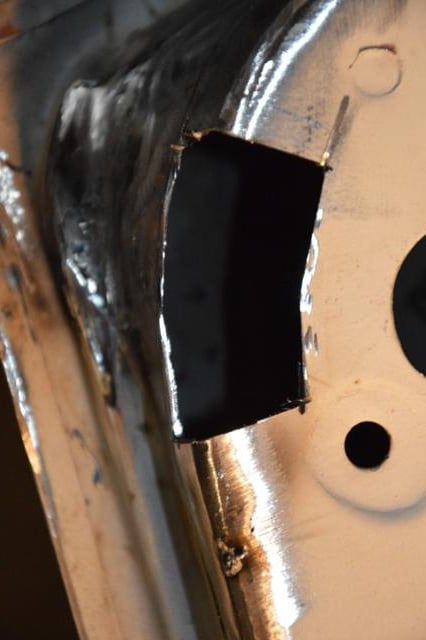
Not the right angle but that bit is 2mm of steel the center is about 1.5mm ish give or take 1/4 of a mm
so i bend the 90 degree angle in it thinking it would then be eaier to bend the smaller bend thing bend up in the bend thingo.
After trying with a couple of pairs of plyers and getting one of the sides bent and the other one more or less flat. I went ape with theorys.
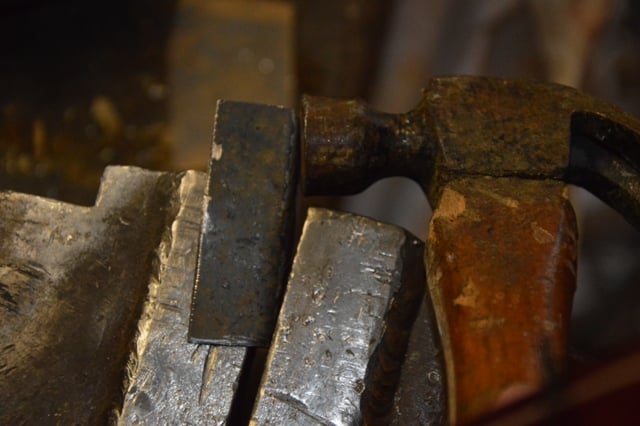
So i tried doing this, as you can see tis only bending the one edge.
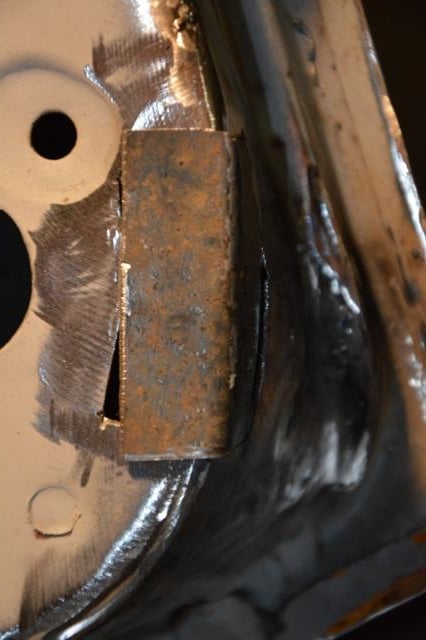
The bottom is good, rest isnt.
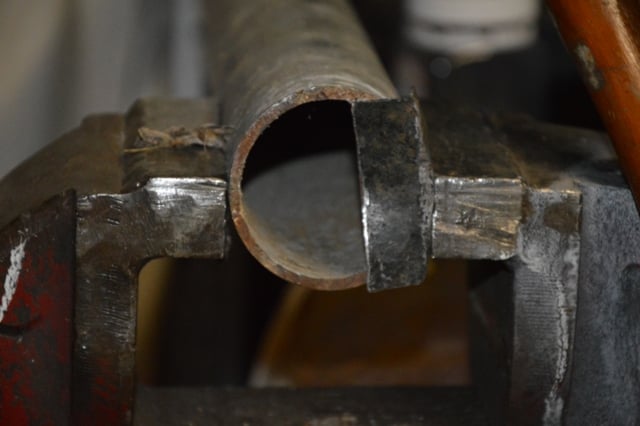
THEN i tried doing this, also didnt work.
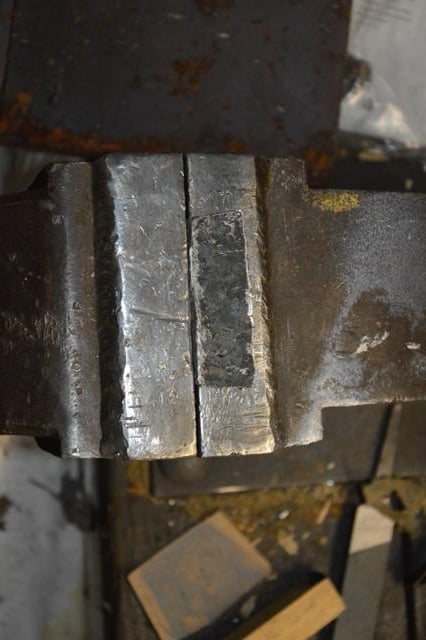
so i put it in the vice and smashed the shit out of it and gave up for the day! 
so question time.
Can i do 2 sections and join them on the bend with weld or is that a no go cause it would be structuraly not so good?
Im assuming you would do this is one of those 2 wheel thina majigas, would be it worth making a rough fail version of one of them if question 1 is a no go.
Also i dunno y but some of the images have flipped themselves over so.......yea photobuckets playing tricks on me.
Edited by Hamster, 29 August 2013 - 04:19 PM.