
Floor pan replacement help
#26
_Bomber Watson_
Posted 07 November 2010 - 05:20 PM
Gongs method although better is only really good for experienced welders.
Cheers.
#27
_SnotGobbler_
Posted 07 November 2010 - 05:37 PM
Honestly mate the reason i suggested you have an overlap is because you said you were only a novice welder....Far easyer with an overlap and even if your welds are a bit hows ya momma it should be strong enough.....
Gongs method although better is only really good for experienced welders.
Cheers.
yeah, i figured that. ill see how it goes after more practice. im in no hurry at this stage
as for a piece of copper, was reading bout that last night.. or a chunk of aluminum apparently.. but i have neither
trying to think of where to find some
thanks for all the feed back
#28
Posted 07 November 2010 - 06:02 PM
This is pointless and messy.
Concentrate on only grinding the weld and you will achieve a much better result.
All grinding the parent metal away does is make it thinner and weaker.
Not bad for a beginner,though.Keep at it as practice makes perfect.Full points to you for jumping into the deep end and doing it the hard way.
Always aim for perfection and try to improve your methods when something gives less than perfect results and your work can only get better.
If you practice quality work,it will become habit.
No doubt some of you will disagree with this comment,dribbling crap about bog filling the grinding divots or sound deadener covering it up.
You are wrong.It is just poor workmanship.
End of story.
rant over,sorry bout that......

#29
_SnotGobbler_
Posted 07 November 2010 - 07:12 PM
I see when you grind you have attacked the parent metal as well.
This is pointless and messy.
Concentrate on only grinding the weld and you will achieve a much better result.
All grinding the parent metal away does is make it thinner and weaker.
Not bad for a beginner,though.Keep at it as practice makes perfect.Full points to you for jumping into the deep end and doing it the hard way.
Always aim for perfection and try to improve your methods when something gives less than perfect results and your work can only get better.
If you practice quality work,it will become habit.
No doubt some of you will disagree with this comment,dribbling crap about bog filling the grinding divots or sound deadener covering it up.
You are wrong.It is just poor workmanship.
End of story.
rant over,sorry bout that......
Funny man.. when i was grinding down the weld and taking out the parent metal..the thought going through my mind at the time was wondering if someone would pull me up on that so good spotting
and you are right.. i just couldnt be bothered being fussy as it was scrap
#30
Posted 07 November 2010 - 07:30 PM
Don't grind in one spot till you get the blue, be patient and keep moving.
Matt
#31
_markm_
Posted 07 November 2010 - 07:50 PM
#32
Posted 07 November 2010 - 08:01 PM
Flap wheel?
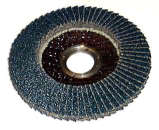
#33
_SnotGobbler_
Posted 07 November 2010 - 08:27 PM
why is flap wheel better?
from memory, i cleaned up the sill welds by taking off the top of the weld, then finishing it off with a sanding disc under advice of me panel beater
so i was going to do the same with all other welds
#34
_Bomber Watson_
Posted 07 November 2010 - 10:47 PM
But yeah he's right, try not to touch the Parent material.
I kinda disagree with the flapper thing though, they put to much heat in and take to long, take the top off with a grinding disk, just go till you can feel a slight ridge, then hit it with a sanding disk/flapper wheel. I prefer sanding disks as they offer a better feel of the job.
At all times during the grinding/sanding process you should be able to rest your hand against the area and not get burnt. If you get burnt its to hot, and you will have a nice blister to remind you about it.
Cheers.
#35
_BATHURST-32D_
Posted 08 November 2010 - 06:16 AM
I kinda disagree with the flapper thing though, they put to much heat in and take to long, take the top off with a grinding disk, just go till you can feel a slight ridge, then hit it with a sanding disk/flapper wheel. I prefer sanding disks as they offer a better feel of the job. i also agree
you need to use your welder as a spot weld or you will get to much heat in there and warp your floor, if you spot about every 2 inches to start with working from side to side and moving all over the job at the end it will be a better and easier to clean job,
your local scrap yard will have the copper or ally you need man.
be patient. this is the key
and all the above is only if you want your car to look perfect from the underside, a little advice would be make sure you leave some neat weld under your carpet on the inside of the car so you dont grind the bottom to thin, you will really need a hoist or rotissori for this job 2 b done to its best.
keep at it and good luck
cheers gong
Edited by BATHURST-32D, 08 November 2010 - 06:31 AM.
#36
_BATHURST-32D_
Posted 08 November 2010 - 06:38 AM
You are wrong.It is just poor workmanship.
End of story.
and this comment from watty was spot-on
cheers gong
#37
_2runa_
Posted 08 November 2010 - 11:18 PM
I agree with Gong but Everyone has slightly different approach, whatever works for you so long as it leaves a good result. I use a 2" angle grinder yes a 2" then a 2"sanding disc both are exellent to feather in the welds with a greater controlNo doubt some of you will disagree with this comment,dribbling crap about bog filling the grinding divots or sound deadener covering it up.
You are wrong.It is just poor workmanship.
End of story.
and this comment from watty was spot-on
cheers gong
#38
_73LJWhiteSL_
Posted 09 November 2010 - 11:59 PM
Thanks to all for the comments. Great reading. I will revisit this before i hit the LC.
Steve
#39
_SnotGobbler_
Posted 10 November 2010 - 06:12 PM
Great Thread SnotGobbler, its really encouraging to see someone having a go. I have been playing with a mig for the last few months on and off ( have maybe 4 or 5 hour practise) just welding crap together. I will be moving to thinner stuff soon (1mm steel and then rusty car doors from the wreakers) before i begin my LC Coupe.
Thanks to all for the comments. Great reading. I will revisit this before i hit the LC.
Steve
thats good to read
just make sure its good crap your practising on lol
shouldnt take long if you do it enough.
i guess ive only done a couple of hours so far. welding 2mm was easy enough, so much more to it with 1mm.. but we'll get there
got a spare door to work with next
good luck and have fun
#40
_JNR_ATE_
Posted 17 April 2012 - 11:07 PM
gradually lower the amps and wire speed and attempt to creat the same constant weld, your aiming for good penetration(insert joke here).
Thicker steel will alow you to weld without blowing a hole in it.
Try that
Cheers
JNR_ATE
wow, just realised the date on the last post, hope he learnt to weld, lol
#41
_whiked27_
Posted 10 November 2016 - 08:45 AM
Does anybody know if you can use front floor pans in the rear? 75 LH or know of anybody that makes the rear ones?
#42
Posted 11 November 2016 - 09:28 AM
From memory no one makes replacement pans keep a lookout for good secondhand ones.
#43
Posted 11 November 2016 - 08:28 PM
1 user(s) are reading this topic
0 members, 1 guests, 0 anonymous users