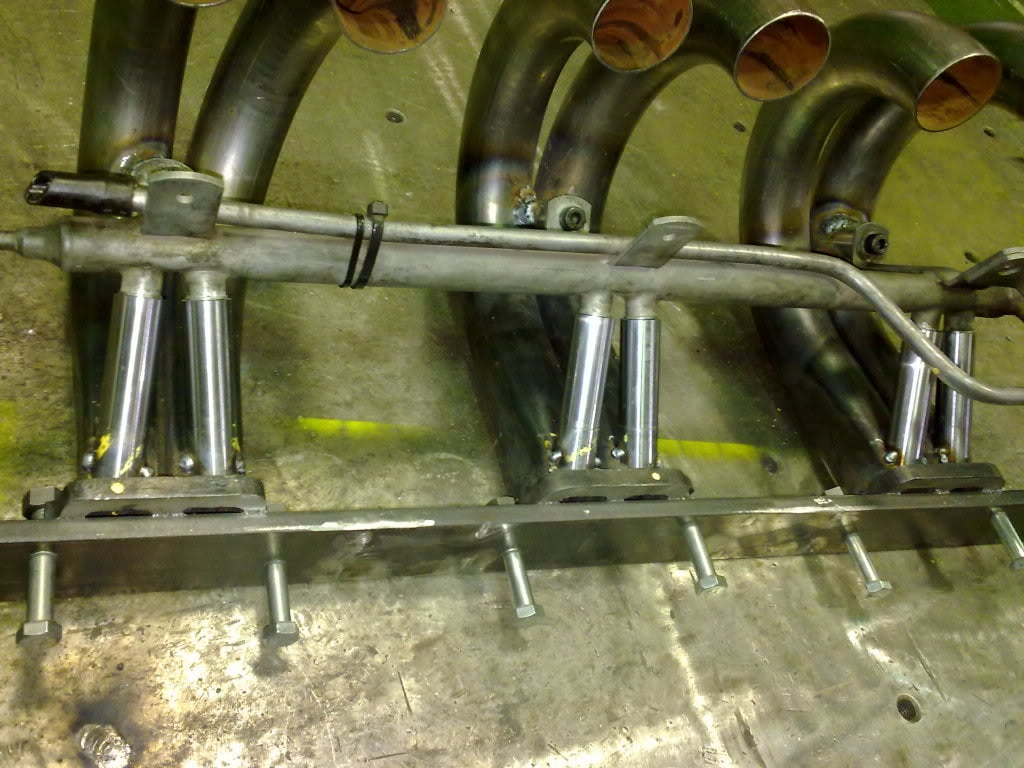
Ground the bosses flat
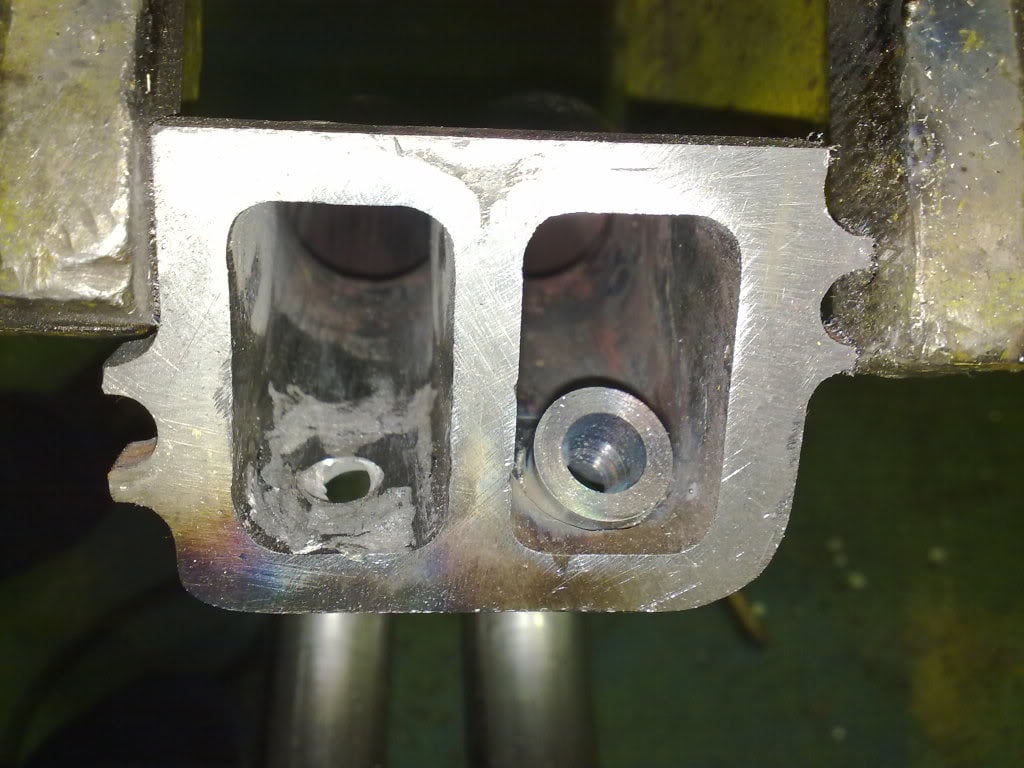
Made it look a little neater
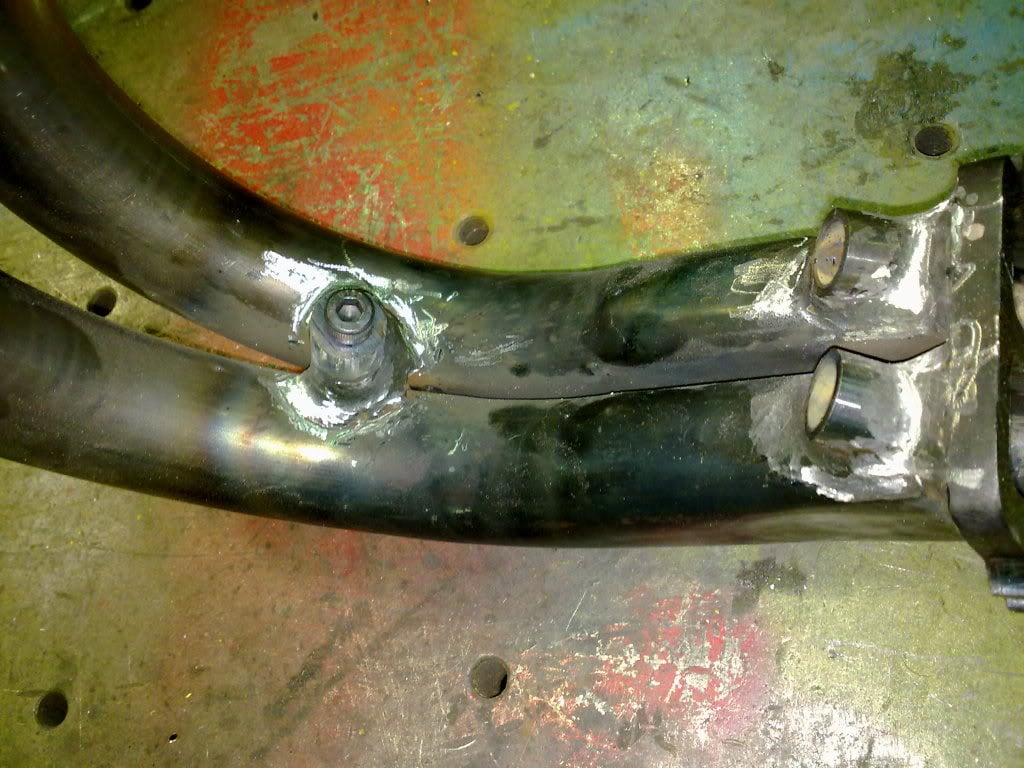
repeat 3 times and its almost ready for the plenum to be made.
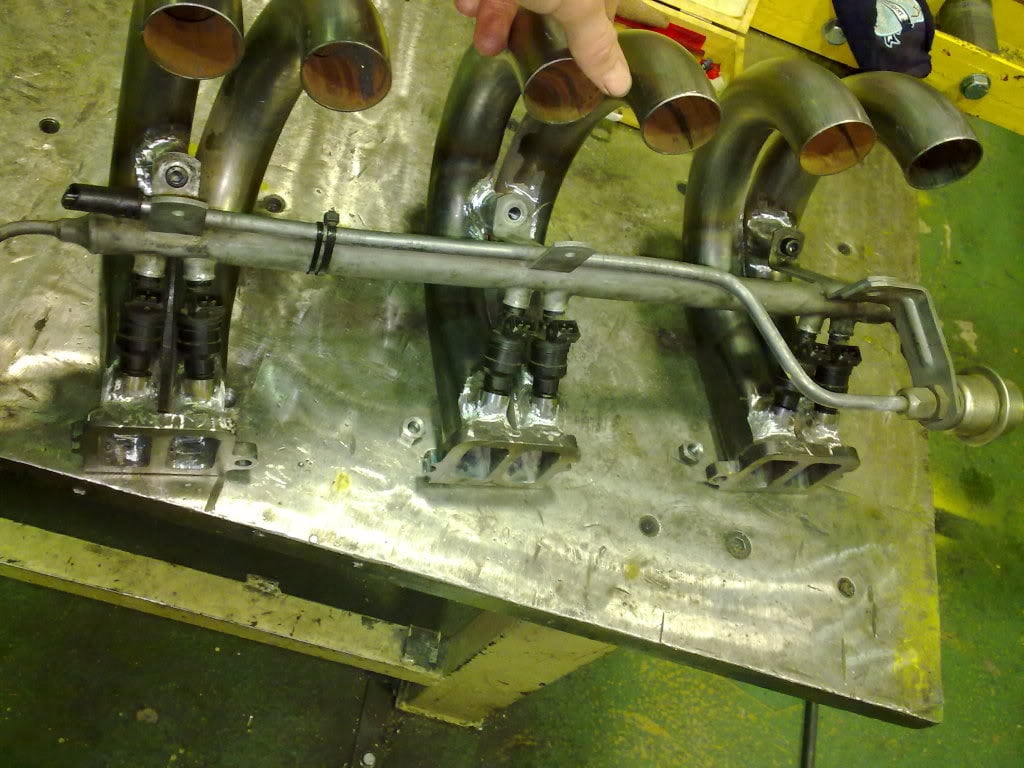
Posted 10 August 2011 - 07:40 PM
Posted 10 August 2011 - 07:43 PM
Posted 11 August 2011 - 01:15 AM
Posted 11 August 2011 - 08:48 AM
Posted 12 August 2011 - 12:53 AM
Can't wait to see this run.
How did you determine the volume of the plenum?
Posted 14 August 2011 - 08:57 PM
Posted 19 August 2011 - 05:32 PM
Posted 02 September 2011 - 05:57 PM
Posted 02 September 2011 - 06:03 PM
Posted 02 September 2011 - 06:08 PM
Posted 02 September 2011 - 06:57 PM
Posted 02 September 2011 - 09:39 PM
Posted 05 September 2011 - 08:19 AM
That is absolutely awesome mate... Top stuff!! How will the throttle response etc be on it you reckon?
Posted 05 September 2011 - 09:17 AM
Posted 05 September 2011 - 10:10 AM
From what ive found plenum volume should be 100% of engine compacity for N/A and 150% for engine capacity for Forced Induction
The way you have your throttle body setup id say the air will shoot straight down port 3 and 4 and you wont get as much down 1,2,5,6.
Posted 05 September 2011 - 10:44 PM
Posted 27 September 2011 - 01:18 AM
Posted 27 September 2011 - 08:24 AM
Edited by Viper, 27 September 2011 - 08:27 AM.
Posted 27 September 2011 - 09:56 AM
I wish I knew more about flow testing. Does the flow bench pull more or less air than the motor is capable of drawing? ie. a slight flow drop at 28" equals a massive difference at 6,500RPM or bugger all?
Posted 27 September 2011 - 10:56 PM
Posted 28 September 2011 - 12:44 AM
I have been planning to rebuild my 202 and get it all set up for lpg injection. I was looking at making a custom manifold for it. This is exactly what I had planned on making, with the exception on a front facing TB instead of side. I am extremely intrigued in the wedge that you have. Is this something that you have made or can it be purchased etc?
Posted 30 September 2011 - 12:53 PM
Posted 30 September 2011 - 01:13 PM
Posted 04 October 2011 - 12:39 PM
I don't think you're going to get much better than this without making the runner diameter excessively big.
To keep it in perspective it's flowing a whopping 25 - 30cfm more than the VK manifold. The potential is definitely there to make some good, yet streetable, torque and hp numbers.
Was there no test of 3 or 4?
Posted 04 October 2011 - 01:16 PM
0 members, 1 guests, 0 anonymous users