Take one HQ guard, this one is is a fair bit of a mess, going to take alot of repair work to get it straight again
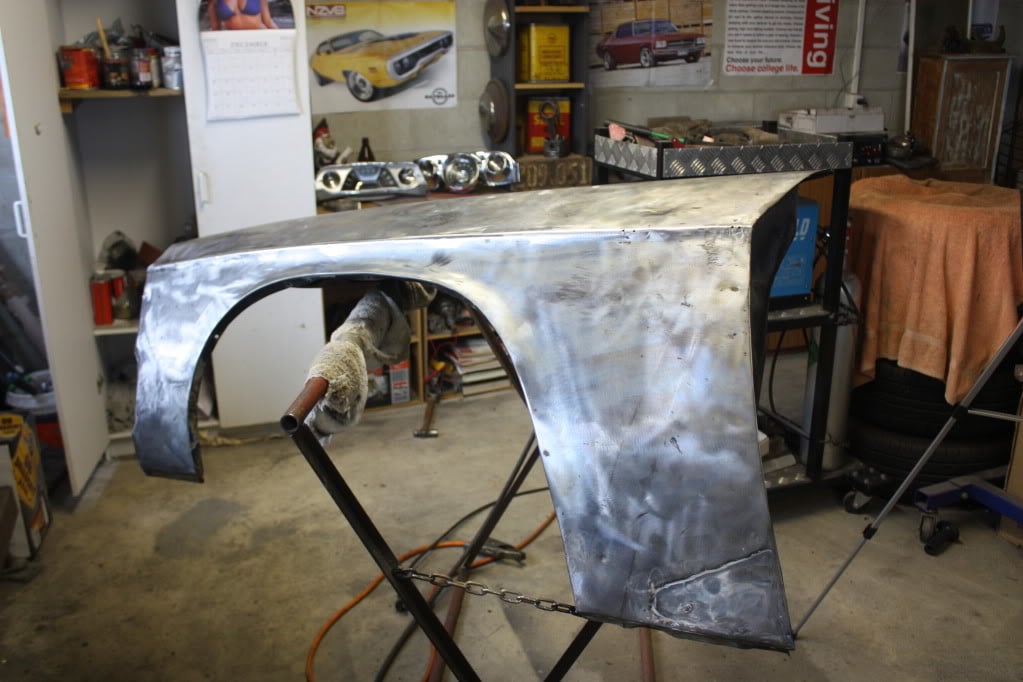
Holes for trim (plus a few extras). First step is to ensure the swage is straight around where you are going to weld. Mig isnt all that forgiving when it comes to planishing
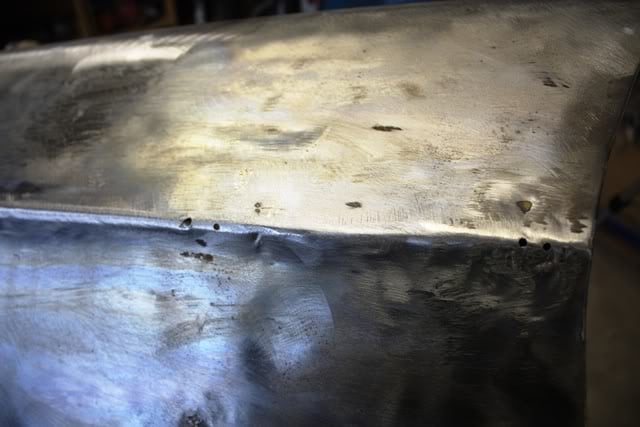
Much better
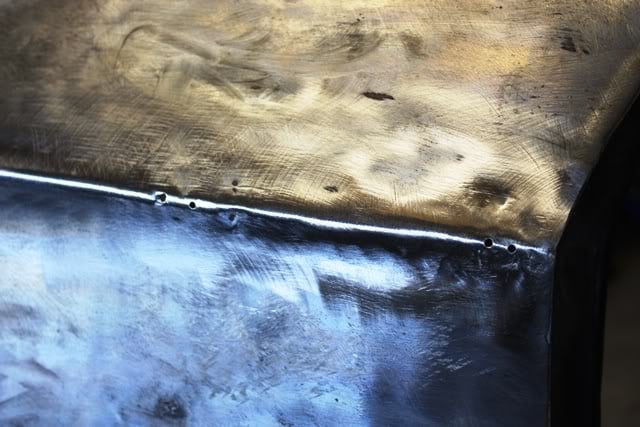
This helps alot, take your pick hammer, sit it in the back side of the hole and hit the face end with another hammer. This will flare out the otherside and help prevent any undercutting when you go to run the weld

Like so
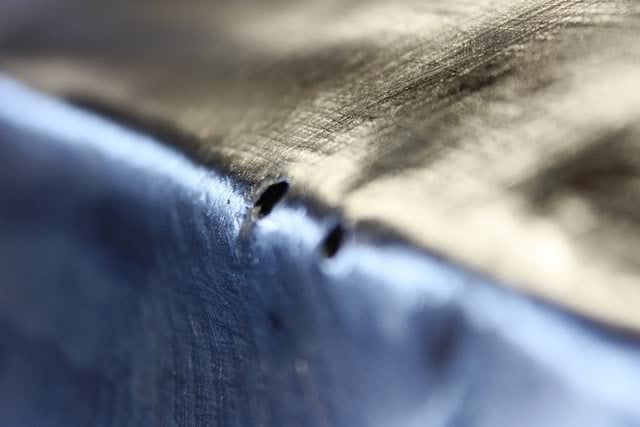
Take a strip of copper (or alloy) and hole it on the back side of the hole so you have something to weld against
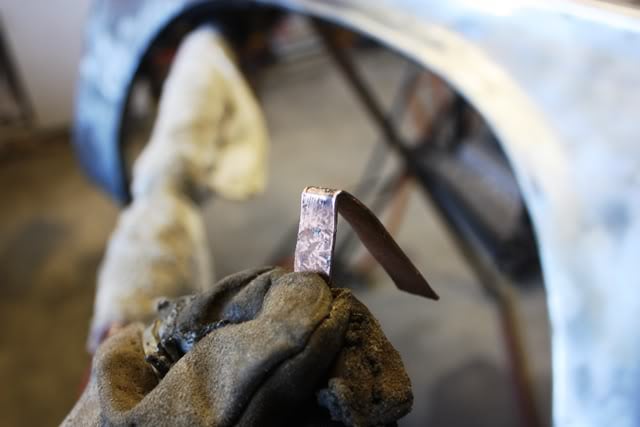
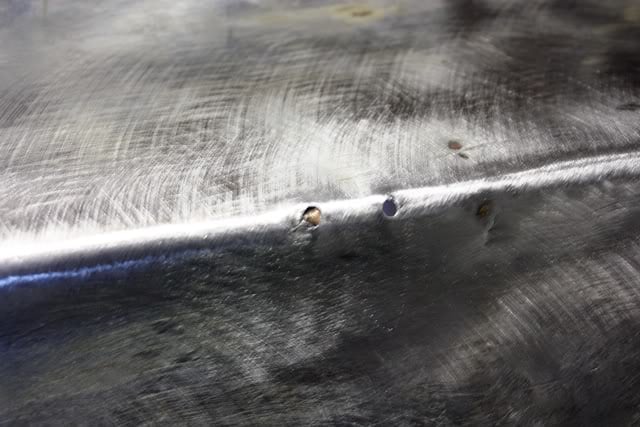
Weld. I usually do it as a couple of spots and melt the lot together in the final pass. Give yourself plenty of 'crown' on the weld to grind back
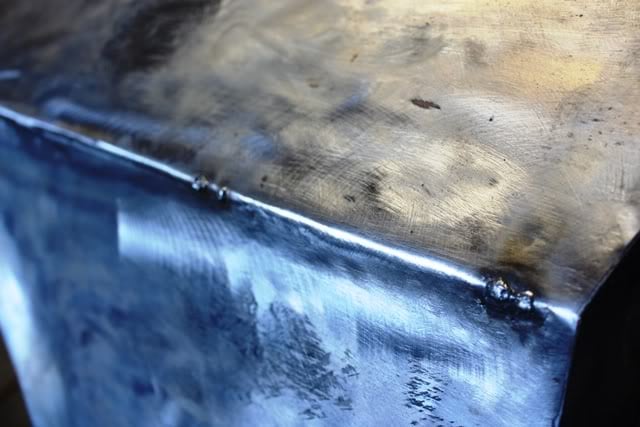
Grind back with a flap disc or sanding disc, only go along the swage not across it so you dont create a hollow
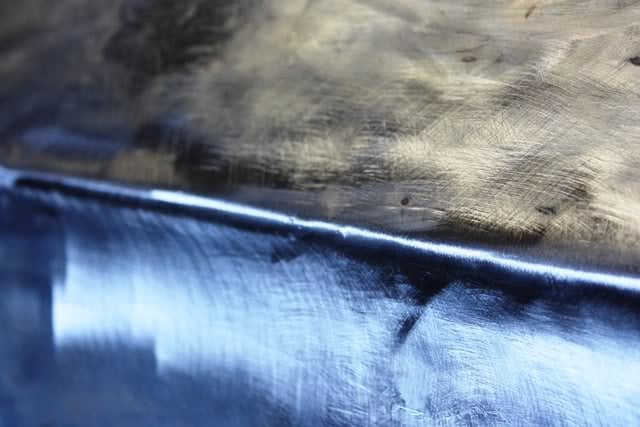
Spot the weld?
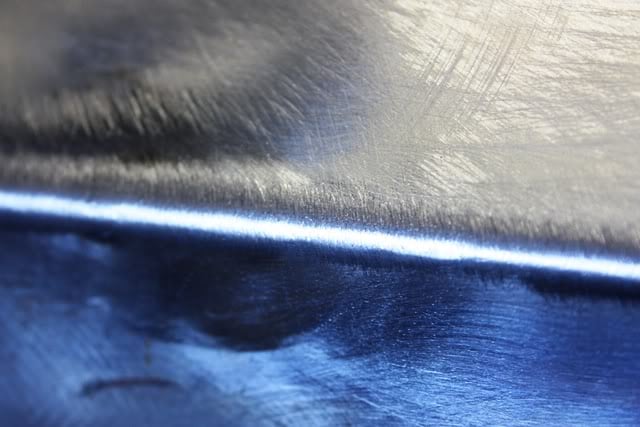
I go across with a panel file just to get rid of any highs and make sure the line is still there
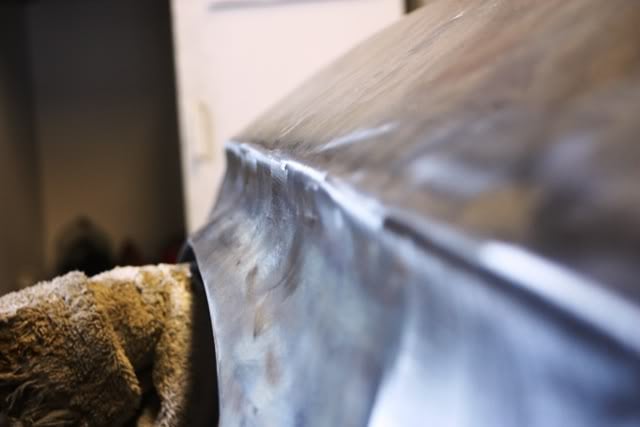
Happy welding

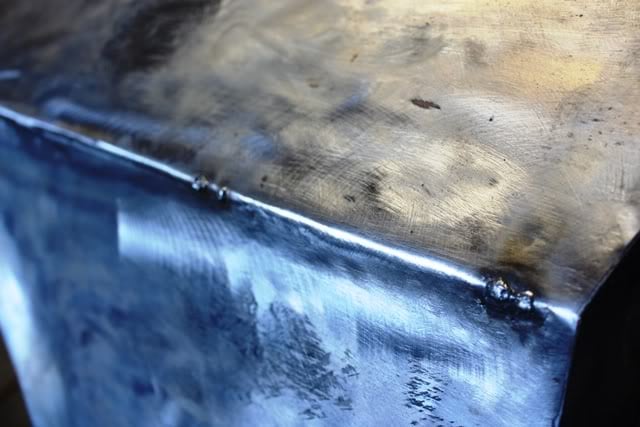