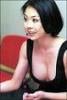
#1
Posted 04 May 2013 - 02:39 PM
The coating is looking a bit the worse for wear with some flaking and rust.
I am looking at getting another set done and was wondering what people's long term experience has been with other high temp coatings on exhaust manifolds. I am of course looking at shiny rather than flat colours.
#2
_shan620_
Posted 04 May 2013 - 02:58 PM
#3
Posted 04 May 2013 - 03:28 PM
I think any coating, in the extreme heat conditions extractors face (exhaust heat at around 600 to 1000degC when it leaves the head) and the 0 to 10Deg C cold coming up off the road (rain/hail, cold weather) will put any coating to the test, I doubt you will find anything will stand upto it, especially in the collector area where it is closest to the road.
#4
Posted 04 May 2013 - 05:41 PM
#5
_cruiza_
Posted 04 May 2013 - 06:07 PM
I did 120,000km with my extrators (Pacemakers) in my hatch, drove in rivers on beaches and in all weathers from snow to heat and after they lost their intinal shine they were much the same when I sold the car as when I first put them in.
the coating I used that work so well.... none cost me nothing took no time and worked a treat
#6
Posted 05 May 2013 - 09:24 PM
They lost their shine, but never the coating integrity. As far as I know they are still going strong.
#7
_chrome yella_
Posted 06 May 2013 - 11:04 AM
i had my L34 headers done by JET HOT about 4 yrs ago, no probs . I got mine done in flat black which turned out great because they still have to do the same process as the shineys but it gets the extra baked coat of black on top.
#8
Posted 06 May 2013 - 03:46 PM
You know you can polish it if its still in good nick, comes up ok.
#9
Posted 06 May 2013 - 04:50 PM
#10
Posted 07 May 2013 - 08:36 AM
I tried polishing mine, didnt seem to make much difference and they put off a weird smell when being polished (well they did with mirror finish and purple polish)
#11
Posted 07 May 2013 - 09:16 AM
Start with brasso, then move to a good mag wheel polish.
#12
Posted 07 May 2013 - 05:57 PM
To re-polish any of the ceramic chrome like coatings try polishing with either "Autosol" aluminium polish or "Mothers" mag & wheel polish.
It is the aluminium powder mixed through the ceramic coating that makes it look shinny in the first place.
Polish with a clean rag and in small areas at a time.
Once you have finished polishing make sure you wipe the pipes down with thinners or acetone after polishing to remove the last bit of the polishing compound.
Otherwise the surface can turn yellow and stain when they get hot again.
Use standard white kitchen paper towel so you can see that you have removed all of the polishing compound with the solvent.
Left over polishing compound looks black against the white paper towel.
For tarnished area or hard to remove burnt on oil stains on the pipes you can use "OOOO" or 4/O grade steel wool on the affected areas.
Do not push too aggressively, polish lightly using the steel wool in a circular motion in the area to remove the stain only.
Most of these coatings are very thin and it is easy to polish through them, so be careful.
Then once you have finished with your steel wool polish finish with the aluminium polishing compounds as mentioned above.
Definitely do not use any type of steel wool on black, grey and other solid coloured ceramic coatings.
If the ceramic chrome looks like a dull grey or is flat and discolored, especially for the first four to six inches from the exhaust ports or on sharp bends then this is a good indication that the aluminium powder in the coating has burnt and the coating has failed. The pipes will need to be stripped and re-coated again.
Regardless if the ceramic chrome coating has come from HPC, Jet Hot, Techline or Cerakote they all use aluminium powder mixed in a ceramic solution.
The recipe to make this type of ceramic chrome coating is over 25 years old and the shinny look of the coating has more to do with the person applying the coating, the original condition of the pipes, how it is applied and polished than the actual brand of coating that you use.
The upper limit of the ceramic chrome as a single coat on the exterior of an exhaust pipe fails at approximately 590 deg C (1100 deg F) - this is the surface temperature of the pipe.
So what the ceramic coating shops do is apply a coat of the ceramic chrome coating inside the pipe and a couple of coats on the outside of the pipes to raise the thermal limit of the coating. This lifts the thermal limit to just over 650 deg C (1200 deg F).
So this type of coating would only suit a moderately worked naturally aspirated V8 engine up to 350 hp and stay shinny without discoloration.
Most Holden 6 cylinder engines that have been moderately worked will unlikely burn the ceramic chrome coating.
Keeping in mind that coating failure is linked to temperature rather than engine type.
Coating manufacturers like Techline and Cerakote have different thermal barrier coatings that do not have the aluminium powder content in the coating but are a more pure version of the ceramic without additives and coloured pigments.
These are used as internal coatings and base coats under any of the other coloured or chrome ceramic top coats.
These thermal barriers can be applied inside and outside of the pipes, baked, cooled and etched before applying the ceramic chrome finish over the top.
This multilayer method lifts the thermal limit of the ceramic chrome coatings to just over 800 deg C (1500 deg F).
In comparison the Black, Titanium, and Tungsten coloured ceramic coatings use high temperature ceramic based pigments in the ceramic matrix so the upper temperature limit of these coatings often exceeds 900deg C (1650 deg F).
When these higher temperature solid coloured coatings are applied over the base coats and combined with the internal thermal barriers these coatings can often reach upper limits of 1200 deg C (2200 deg F).
These are the best choice for high performance applications like hot street cars, race engines and any moderate to high boost turbo engine applications.
The down side to double and triple coating of pipes in different products is they become more expensive to apply because each coat needs to be applied, baked, cooled and etched before the top coat can be applied baked and cooled again. It is like applying the coating twice over.
So as nice as the ceramic chrome coating looks it has some thermal limitations.
#13
_LXSS350_
Posted 08 May 2013 - 01:44 AM
Beans that was an excellent explanation.
#14
_judgelj_
Posted 14 May 2013 - 01:35 PM
#15
Posted 14 May 2013 - 05:50 PM
Best to get a quote from some local VIC ceramic applicators.
The cost will depend on exhaust type (cast manifold or tubular headers), length and type of coating required.
You could try some of these guys.
High Octane Coatings - Langwarrin - 0401 747 184 (Matt)
Jet Hot Coatings - Castlemaine -(03) 5470 6416 (John)
HPC - Leongatha - (03) 5662 4719 (Chris)
#16
Posted 15 May 2013 - 04:26 PM
#17
_judgelj_
Posted 16 May 2013 - 11:11 AM
#18
Posted 16 May 2013 - 02:02 PM
Have a look at the data on the links below.
Ceramic V Heat Shield - http://www.cerakoteh...dHeatShield.pdf
More testing here - http://www.cerakoteh...mp.com/testing/
According to the data the ceramic coatings are on average 3% more efficient than heat shielding the pipes. So there is not much between them.
This is based on a single top coat of light metallic grey ceramic (see test report) on the exterior of the pipe.
You would get a better results (if you needed it) if you were to double and triple coat the pipes as I mentioned in the above post.
The benefits of the ceramics are their ability to resist repetitive thermal cycles (heating and cooling) they have good corrosion and chemical resistance.
Not many chemicals effect the finish of the ceramic coatings (except soaking in Phosphoric based acids).
Heat wrapping can also creates overheating of the pipe by not allowing the heat to dissipate, it soaks into the pipes and has them glowing red like we see in the you tube videos.
Except you cannot see this because it is under the wrap.
This causes metal fatigue as the temperature super-heats and cools the steel in the areas where the wrap is not allowing the heat to escape or be re-directed down the exhaust.
On the flip side the ceramics act as thermal barriers that resists the heat from soaking through the pipe allowing the heat to travel down the pipe and out through the exhaust.
This is a bonus in turbo applications were you want to keep the energy from the exhaust spooling the turbo.
This thermal barrier performance of the ceramic coatings also reduces radiant heat from the exterior of the pipes and reduces engine bay temperatures.
Another down side to heat wrapping is the potential for it to become a fire hazard.
Over time, if engine oils and fuels are allowed to soak into the wrapping these can ignite and cause a fire.
The benefit of heat wrapping is its lower price and that it can be done at home and re-applied if it requires servicing.
If you are not overly concerned about the look of your fuel bowls (do not have to have a chrome look) the Cerakote people offer an air cured range of solid colour ceramics (including silver) that can be sprayed directly onto parts by the home user.
This may be an option for creating a thermal barrier around your fuel system.
Many V8 racing teams often ceramic coat the underside of their intake manifolds to take advantages of the thermal barrier properties of the ceramics to keep the air/fuel as cool as possible. They also have gloss and matte clear ceramics that can be applied over polished surfaces for a similar result.
#19
_judgelj_
Posted 16 May 2013 - 03:33 PM
Wow, what a wealth of info. Ill probably look further into ceramic coating as it seems to have many more advantages. Ill leave it there as i dont want to hijack this thread any further.
Cheers
#20
Posted 30 May 2015 - 06:13 PM
I have fitted a new exhaust with coated pacemakers and first run the exhaust smokes like a Mitsubishi!
I am guessing this will pass after a while, any experiences from those who have fitted them?
#21
_judgelj_
Posted 31 May 2015 - 12:16 PM
didnt with mine.
#22
_Mint_
Posted 31 May 2015 - 01:59 PM
I had them in the car fitted to a new motor and on first start up and cam break in they burnt..went dull
in hind sight I should have had a workshop fan blowing on the motor to help keep them pipes cool or another way would be to run the cam in on an engine stand with standard manifolds
just something to remember
#23
_Bomber Watson_
Posted 31 May 2015 - 04:24 PM
#24
_judgelj_
Posted 31 May 2015 - 05:20 PM
Mine were ok during cam run in, but didnt get that hot. Engine run in does void the coatings warranty though.
#25
Posted 31 May 2015 - 08:46 PM
So what is the best way to "break-in" a freshly coated set of headers?
1 user(s) are reading this topic
0 members, 1 guests, 0 anonymous users