Thank-you, and a dry sump is used in racing engines as you all know, do we still have to have a scavenging system?
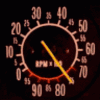
'HOLDEN FLAT or V12'
#101
Posted 30 June 2013 - 08:09 PM
#102
_STRAIGHTLINEMICK_
Posted 30 June 2013 - 08:31 PM
If a simpler system couldnt be found then i think the dry sump would be the go . What about a fabricated deep sump at the rear , external pickups to each oil pump .I think a good crank scraper is needed to get oil down to the sump 3/4".Drain tubes from rocker covers and along the crankcase to the sump . It might look like a dogs breakfast though ,any suggestions ?
#103
Posted 30 June 2013 - 08:35 PM
Hey DJ,
Would we face the manifold inwards so the carbys are not sticking outside of the Flat 12 width.
Solved the one head up one down problem, get some tomas tripple strom manis and hang su's off them. Three above three below.
#104
Posted 30 June 2013 - 08:39 PM
Be plenty of room for the dry sump below the Engine which can take gravity feed from all parts of the Engine.
If a simpler system couldnt be found then i think the dry sump would be the go . What about a fabricated deep sump at the rear , external pickups to each oil pump .I think a good crank scraper is needed to get oil down to the sump 3/4".Drain tubes from rocker covers and along the crankcase to the sump . It might look like a dogs breakfast though ,any suggestions ?
#105
_STRAIGHTLINEMICK_
Posted 01 July 2013 - 10:35 AM
Yep you could drain into a fabricated reservoir below the engine and have external pickups to the stock oil pumps .or an external pump. reservoir would need to hold about 8 litres for safety and have drains spread around to ensure drainage no matter what forces are acting on it .(With more drains at the rear because of the massive aceleration we all expect )
#106
_STRAIGHTLINEMICK_
Posted 01 July 2013 - 02:10 PM
Hey blokes ,go to youtube and type in 'american austin flat 8 by john owen' this is good old redneck engineering ,I feel like i have looked into the future .
#107
Posted 01 July 2013 - 05:01 PM
Hey blokes ,go to youtube and type in 'american austin flat 8 by john owen' this is good old redneck engineering ,I feel like i have looked into the future .
Nice find Mick,
Yep, he did it, also he has an inspection area for the Crank,
so now you are thinking of doing cast welding,
you could incorporate an inspection area at the top of the right half as there is no oil pump.there. Dave I
p.s. could also cast weld support for the cam area when material is removed for the Main Caps relief as long as it does not distort the bearing retainers
Edited by TORYPOWER, 01 July 2013 - 05:05 PM.
#108
Posted 01 July 2013 - 06:23 PM
Hey blokes ,go to youtube and type in 'american austin flat 8 by john owen' this is good old redneck engineering ,I feel like i have looked into the future .
http://www.youtube.c...h?v=buZMpx2A3es
#109
_STRAIGHTLINEMICK_
Posted 01 July 2013 - 09:32 PM
Nice find Mick,
Yep, he did it, also he has an inspection area for the Crank,
so now you are thinking of doing cast welding,
you could incorporate an inspection area at the top of the right half as there is no oil pump.there. Dave I
p.s. could also cast weld support for the cam area when material is removed for the Main Caps relief as long as it does not distort the bearing retainers
Yes there is an inspection area ,but how will that help our project ?,I still think welding bosses to the blocks is a much neater solution . You will need to use both oil pumps if you go that way .
#110
Posted 01 July 2013 - 10:00 PM
What's the fun in that?Mate I'm not trying to be a party pooper, just trying to be realistic.
I used to average about 20 -25 hours a week of cast iron welding for 35 years. A big oven to pre heat stuff made life a lot easier.How good is Cast welding, other wise a Great Idea Mick
#111
Posted 02 July 2013 - 01:33 AM
Thank-you Mick and Vick for clearing up those points,
Well then, we are getting into short listing how a 'Flat 12' is to be assembled,
There is a bit of concern having a distributor underneath the engine,
that the work in rotating the head 180° may not be such a bad idea as the leads from a 12 point cap as Oldjohnno said, on one distributor can feed both heads.
Would in-different lead length cause any spark dramas?
Other wise have a protective guard under the Engine. Dave I
p.s. I like the idea of keeping as many parts off the shelf in such a project
p.p.s. we could also have the inlet exhaust at the top as mentioned earlier, if the head was turned which would look good / symmetrically / breathe with gravity / exhaust vertically and the guarded distributor under the Engine
#112
_STRAIGHTLINEMICK_
Posted 02 July 2013 - 08:05 PM
It would definatley look better with the inlets at the top ,have you looked into whats is needed to turn a head around ? Pushrods ,and where would the valves be in relation to the bore and the rockers.
If you were actually going to build one i would keep it as simple as possible and change things later once you are confident with it.That means stock dissys ,oil pumps (unless you already have an external pump),water pumps ,i would even make 90 deg adaptors for stock carbs .stock exhaust manifolds also.
You can even bolt a bellhousing to the stock position to mount the starter .
#113
Posted 02 July 2013 - 09:07 PM
Use a VK EST setup on the crank and a VN V6 coil pack arrangement as the basis.There is a bit of concern having a distributor underneath the engine...
#114
_Bomber Watson_
Posted 02 July 2013 - 09:42 PM
I havnt looked at a six head for this specific purpose, but i've seen a lot of them, and im pretty confident it would be damb near impossible to spin it around. To the point it would be eayser to make a new head.
#115
_oldjohnno_
Posted 03 July 2013 - 07:30 AM
Exactly, it'd be easier to fit an OHC head.
If anyone is serious about building one of these it might pay to take a step back at this stage and ask what is it going to be used for, and then design around the answer. Just as you would for any normal engine. It'd be enormously wide, and with one set of manifolds on top and one underneath it'll be pretty high as well. And if it was fitted to some sort of vehicle the manifolds are probably going to be lower than the bottom of the flywheel, as might be the bottom of any "sump". Of course all this wouldn't matter if it was just going to sit in a test stand and sound nice. I can't think of many vehicles apart from a digger or an altered where such a huge package could be fitted behind the front axle and overhanging the frame rails. Possibly tilting it slightly might help with ground clearance.
The other thing is how much power do you want to make with it? You could get away with all sorts of horrible short cuts with the aforementioned engine on the test stand that just has to look and sound the part. But if it needed to make power you'd obviously have to go to a lot more trouble structurally speaking. If you can somehow tie the whole mess strongly together you could jam it into something like a FED. With a 6:71 on top and port injection via log manifolds, and short stub exhausts you'd be able to minimise the bulkiness of the manifolds and the engine overall.
#116
Posted 03 July 2013 - 11:08 AM
#117
Posted 03 July 2013 - 01:24 PM
Thank-you Oldjohnno, Mick, Vick, DJ and 76lxhatch,
I read a few times with the head turning and looks to be a myth for a running engine as DJ said it would be too much to be done than it is worth, here is a link of a ford cross-flow head on a red six:-
http://oldholden.com/node/97157
but the ford head makes the Engine too wide as too the overhead cam idea if it were to go in anything with a 'K' frame.
The WB Tonner has 700mm to play with in which 50 mm would have to be removed from each side, but as Oldjohnno has stated the manifold etc makes it bulky top and bottom.
Looks like having to shift a lot of parts around or making it into a 'V' shape / reversing one motor / weldind etc to even get close. Dave I
Edited by TORYPOWER, 03 July 2013 - 01:25 PM.
#118
_STRAIGHTLINEMICK_
Posted 03 July 2013 - 06:09 PM
Exactly, it'd be easier to fit an OHC head.
If anyone is serious about building one of these it might pay to take a step back at this stage and ask what is it going to be used for, and then design around the answer. Just as you would for any normal engine. It'd be enormously wide, and with one set of manifolds on top and one underneath it'll be pretty high as well. And if it was fitted to some sort of vehicle the manifolds are probably going to be lower than the bottom of the flywheel, as might be the bottom of any "sump". Of course all this wouldn't matter if it was just going to sit in a test stand and sound nice. I can't think of many vehicles apart from a digger or an altered where such a huge package could be fitted behind the front axle and overhanging the frame rails. Possibly tilting it slightly might help with ground clearance.
The other thing is how much power do you want to make with it? You could get away with all sorts of horrible short cuts with the aforementioned engine on the test stand that just has to look and sound the part. But if it needed to make power you'd obviously have to go to a lot more trouble structurally speaking. If you can somehow tie the whole mess strongly together you could jam it into something like a FED. With a 6:71 on top and port injection via log manifolds, and short stub exhausts you'd be able to minimise the bulkiness of the manifolds and the engine overall.
At the moment its just for fun as an engineering challenge ,and it would be fun to build as well . If i was serious about making power i would do an AFR headed 434ci small block .
As with all engineering projects we would have to first demonstrate the idea will work as simply as possible and then look at the engineering changes needed to make reliable power which would depend on the cylinder heads used . It would be ok in a rear engined digger only because driving through shrapnel doesnt appeal to me .
I think the lthe blocks will have to be dowelled ,through bolted as well as have bosses welded to the outside to make it rigid and then build from there.
#119
Posted 03 July 2013 - 08:34 PM
Might fit in a HQ +
#120
_Bomber Watson_
Posted 03 July 2013 - 08:45 PM
I think it would be most suitable on a ride on lawn mower, purely because a 404ci holden flat 12 powered ride on lawn mower would be sick.
#121
_STRAIGHTLINEMICK_
Posted 03 July 2013 - 09:17 PM
I think it would be most suitable on a ride on lawn mower, purely because a 404ci holden flat 12 powered ride on lawn mower would be sick.
Now your'e talkin
Edited by STRAIGHTLINEMICK, 03 July 2013 - 09:17 PM.
#122
_oldjohnno_
Posted 03 July 2013 - 09:20 PM
Might fit in a HQ +
Possibly. But you'd have to lift it so high to clear the upper inner control arm pivots that the transmission would stick straight through the centre of the dash and you'd have to cut a hole through the rear seat for the tailshaft.... Bomber's on it, as usual.
#123
Posted 03 July 2013 - 09:41 PM
Well if you reckon things might have to be chopped to fit it then, dammit, why not go the whole hog?
Why stop at a flat 12?
Radial 36 might be the go?
#124
_Bomber Watson_
Posted 03 July 2013 - 09:57 PM
Now that would look AWESOME in a ride on lawn mower.
#125
_oldjohnno_
Posted 03 July 2013 - 10:17 PM
frOck the neighbours.
1 user(s) are reading this topic
0 members, 1 guests, 0 anonymous users