Just out of interest, if I were to build a jig and custom make my own control arms, what would it take to get them engineered?
Would I need to make a prototype of each first and have some qualified person or company do destructive tests and give me a report?
Would it also need to be x-rayed to assess the quality of the welding or would a visual inspection be enough (or maybe just smashing the crap out of it with a BFH to see if the welds break would do)?
Or could I do my own destructive tests with a hydraulic press and document it myself (video, photos etc.)?
Or would I just go ahead and build everything, then let the engineer look it over afterward?
I'm also wondering how hard it would be to modify the upper spring saddle area of the K-member to accept a proper full coilover instead of this weird hybrid QA1 / Viking spring?
You would need to engage an engineer that is recognised by the DOT in your state. It is up to the engineer to decide what testing is required and at what stages the components are inspected. Testing that is required by the engineers would be need to be supervised by an engineer.
The NSW DOT would produce a list of recognised engineers similar to the list below produced by the WA DOT.
http://www.transport...U_VS_IB_102.pdf
McDonald Bros used Talk Torque Automotive (Bill Malkoutzis) for the report on the HQ-WB Wishbones.
There is some information about Bill Malkoutzis qualifications here.
http://www.goauto.co...A2579330004FA6E
This is the copy of the report I was sent via email. It is a shame the quality of the scan is so bad.
http://ls2lxhatch.co...ments/engineers report on wishbones.pdf
An engineer could specify that the welds are to be x-rayed on each part that is made if the design of the part made a single weld critical.
In the case of the McDonald Bros LCA the engineer concluded that welds did not need to be x-rayed.
The construction of the subject part is basically mild steel tubing, plate, and webs. The welding on the subject part is carried out with a TIG welder and of a very high quality. The design is such that there is a number of welds combined to create any one joint. Hence an error in one weld is unlikely to be repeated on the next, and so built in redundancy ensures the strength of any one joint. After testing there was no evidence of cracking or damage to any of the welds on the supplied test part.
This is one way of fitting a true coilover shock. The car was built by Mitchell Race Xreme who also built the Clark Hopkins Hatch. It would be interesting to find out what spring rate was fitted, the spring wire diameter looks thicker than the 760 lb/in springs.
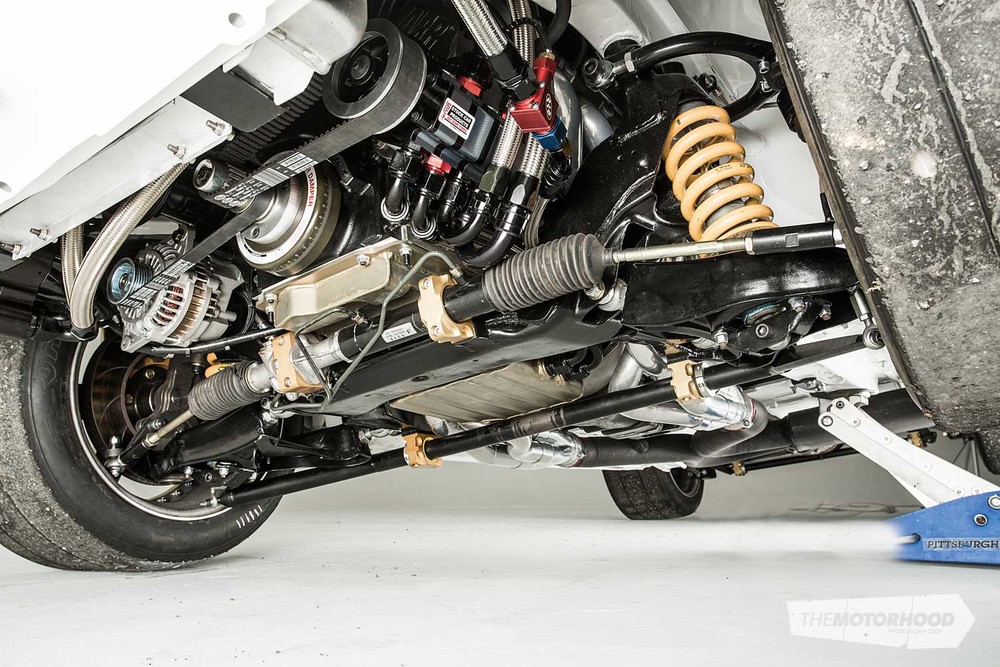
More pictures here.
http://www.themotorh...7-holden-torana
Edited by ls2lxhatch, 11 December 2015 - 11:42 AM.