Yeah you're both right, the only reason im persisting so much is if i dont do it, i feel pretty guilty and incapable. But then again i really cant be bothered. I like the idea of stainless wrap, i might actually do that i have some spare. Though out of curiosity, do we know anyone that sells it by the meter, or roll? Seldom do you come by the kits, at least where i live, and i would want the one size...
It was an absolute prick trying to swap these risers. Took me about 3 trips to the shop to finally understand how it all works and what i needed. Turned out the old risers had a solid bushing AND they were rusted in. So took a while of bashing the riser out, only to require the bushing to be bashed out. Finally got it, fitted the standard rubber mounts and risers.
I bought some more trimmer line this morning so will give it ONE more crack. If not, external wiring it is!!!
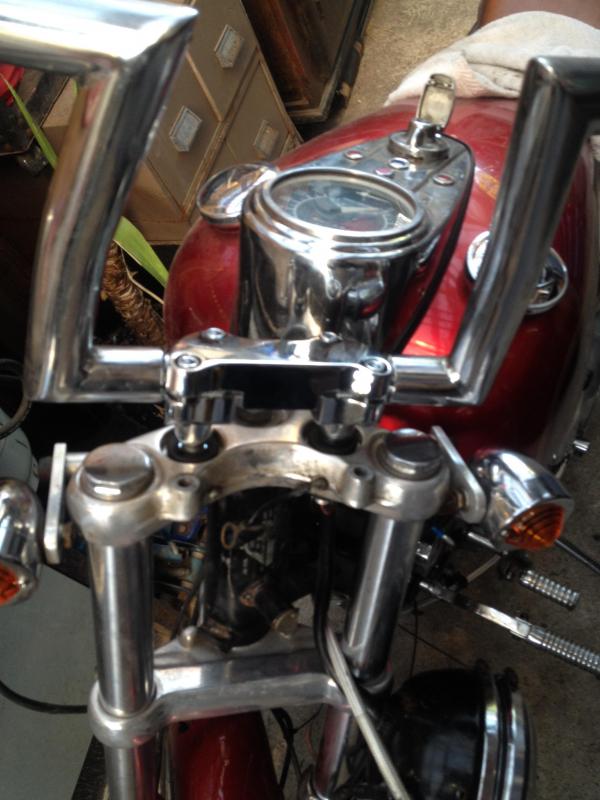
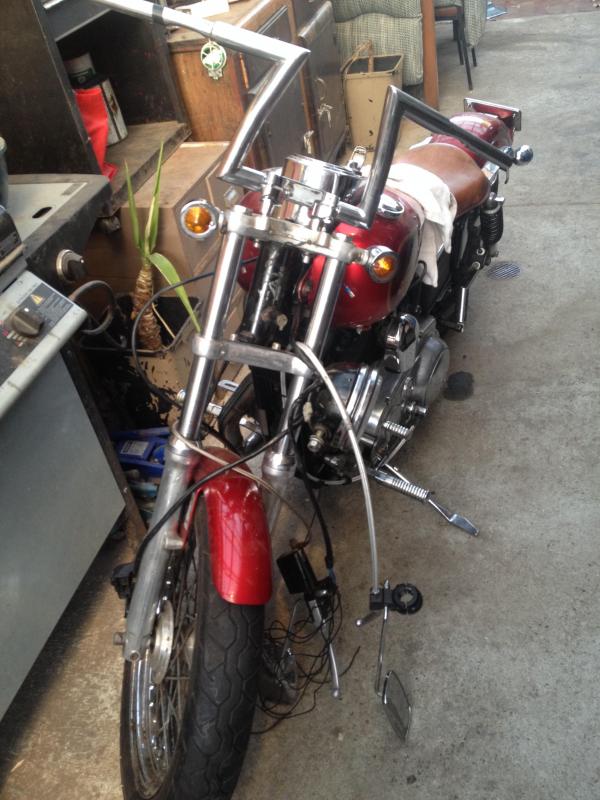
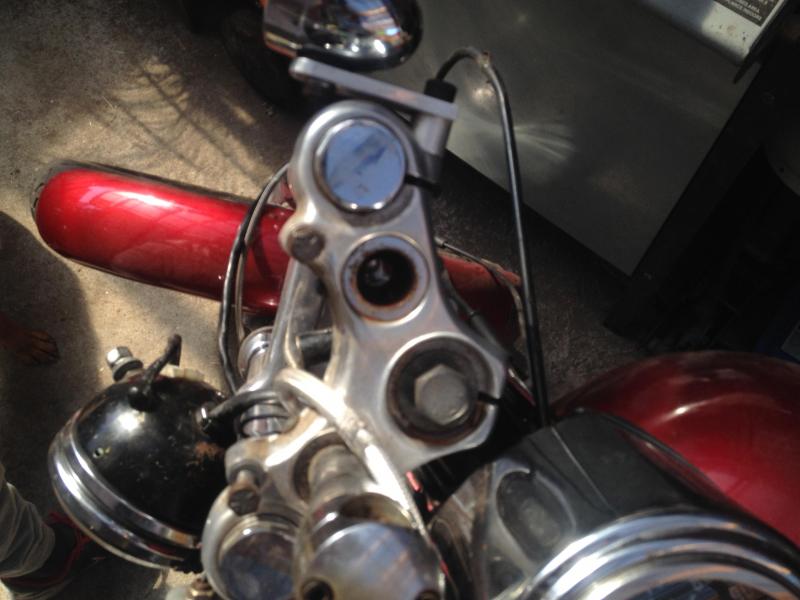