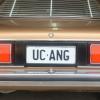
Clutch disengage and spigot bearing q's
#1
Posted 27 September 2015 - 08:08 PM
The clutch, pressure plate and bearing is brand new. The spigot bearing wasn't seated all the way to the back of the crank, would that affect anything?
I also noticed when I pulled the box away from the motor it binded like hell and was coming away on sort of an angle?
I'm going to purchase another spigot bearing and actually check to see whether it fits on the shaft and in the crank - and will press it all the way home.
The pivot ball height is correct.
The new thrust bearing I got I had to remove the old bearing and press the new one into its flange thing that contacts the fork.
I used an array of sockets to align the clutch, might actually go buy a tool and see if that helps.
Any ideas?
Cheers
#2
Posted 27 September 2015 - 08:29 PM
If the spigot bearing isn't seated fully into the crankshaft it is possible it could cause the input shaft to bind against it. This would cause gear change problems even though the clutch is disengaging fully.
#3
Posted 27 September 2015 - 08:48 PM
Is there a better method to getting the spigot into the crank square and even other than using a socket and wailing on it? I wonder if the previous spigot went in properly. I recall the OD of the bush stripping as it was getting pushed into he hole.
#4
Posted 27 September 2015 - 09:19 PM
Genuine or aftermarket spigot bush??? Try your local Holden Dealer. A couple of years ago GMP&A were still servicing the spigot bush, with a bit of luck the Dealer will still be able to get one for you.
Check the leading edge of the spigot recess in the crank for burrs that could cause chaffing or gouging of the outside surface of the bush and round off any sharp edges with some emery cloth.
From memory I used a suitable sized socket to install a new spigot bearing in the 202. Drive the bearing in until you hear the ringing sound of the hammer blow deaden.
#5
Posted 27 September 2015 - 10:40 PM
If you're really worried about it then before you do anything else, dummy-fit the gearbox & bellhousing back to the motor without the clutch & pressure plate fitted (with or without the flywheel bolted up), now reach up through the inspection cover hole and confirm the input shaft spins freely in the spigot?
You could even do this with the existing spigot to confirm whether that was the original problem?
#6
_76lxJAS_
Posted 27 September 2015 - 10:45 PM
spigot bearing fitting.
heat up the crank as much as you can with the heat gun.
have the spigot bush in the freezer for a few hours also before you start heating the crank,
put the spigot bush in while its cold and the crank is as hot as you can
this will help a little for the install,
#7
Posted 27 September 2015 - 11:30 PM
Get the workshop "genuine GMH" manual. There are pages on clutch/pressure-plate/thrust race/spigot installation/bell housing.
Not all spigot bushes are driven home. And there are tricks to getting them out.
They are driven in to a depth specific measurement relative to the crank.
Spigot installing lubrication is same as thrust race.
Use a socket of larger then spigot size to start with and reverse it and use an extension to strike, that will give you a better Idea of driving square.
swap to undersize when you are close.
It ain't that hard!
#8
Posted 28 September 2015 - 06:28 AM
Sounds like you need to check everything with bell housing fitting etc if it was binding. Also make sure that the clutch is not being over-released as some of the hubs are quite large and the diaphragm can end up contacting the driven plate hub and grabbing it.
#9
Posted 28 September 2015 - 07:16 AM
I'll dummy bolt the gearbox with clutch removed and spigot still installed. If it still doesn't slide on or goes in on an angle can we assume spigot bearing?
Also should I bolt the gear selector on once dummy fitted and see whether I can go into gears - will this give me any information?
#10
Posted 28 September 2015 - 10:58 AM
It really sounds like you have 2 problems.
Can you select gears with the box not installed?
centreline the car to confirm, engine- gearbox - chassis alignment, is something bent?
Spigot bush position is a function of input shaft position relative to its protrusion into the crank.
The spigot bush should fully engage the end of the input shaft and not touch the taper to spline area.
I have never seen a spigot bush bottomed out in a crank and it does not seem mechanically logical to do so.
I have seen a spigot bush rammed home (and gouged) by the input shaft because of a butchered installation.
use a clutch plate alignment tool to overcome this problem.
#11
Posted 28 September 2015 - 11:15 AM
Not necessarily, being out of alignment due to bell housing issues or possibly something weird with the input shaft is just as likely.I'll dummy bolt the gearbox with clutch removed and spigot still installed. If it still doesn't slide on or goes in on an angle can we assume spigot bearing?
I'm guessing you still have the original bell housing with separate inspection cover? Get under there and look at it in detail, see which parts are free to move and which are not, you'll soon figure it out.
#12
Posted 28 September 2015 - 01:01 PM
I have never seen a spigot bush bottomed out in a crank and it does not seem mechanically logical to do so.
.
How do you mean 'does not seem mechanically logical to do so'.
#13
Posted 28 September 2015 - 02:54 PM
How do you mean 'does not seem mechanically logical to do so'.
End float on crankshaft and end float on gearbox input shaft, there needs to be room beyond the end of the spigot for the input shaft, plus getting them out if you can't get behind them (easily) when they are bottomed in the crankshaft. GMH would not approve the method of removal I use which is to tap them and insert a rod/washer/nut and wind them out or hydraulic them out with grease and a close tolerance rod and hammer them out.
Besides, GMH don't to anything different unless they have to and if the later spigots are set by depth of the crank ( and not homed) it would be mechanically logical to think all the engineering reasons for that have not changed. Has anyone seen a GMH manual that confirms spigots homed in the crank?
#14
Posted 28 September 2015 - 03:28 PM
The installed depth of the spigot bush has no bearing on and cannot change or alter the physical or installed length of the clutch gear other than to foul the shoulder of the clutch gear splines if the bush is not installed deep enough into the crankshaft.
If you have a look into the spigot bush recess in the end of a crankshaft you will notice the hole is tapered to a point so even though the perimeter of the spigot bush has bottomed on the shoulder in the crank recess there is a deeper void in the centre.
I use grease and an old clutch gear to hydraulically remove a spigot bush. I've also heard of using wet paper balls packed into the bush instead of grease or bolts screwed into the bush or Dynabolts etc etc. To date I have never seen or been able to find any information in any Holden workshop manual regarding removal or installation of spigot bushes, therefore I believe Holden didn't regard it to be important or critical enough to bother to mention.
#15
Posted 28 September 2015 - 09:50 PM
Too far in and you will not be able to use the recommended tool 6A12-2. and was the case when I pulled my gearbox out and found the spigot bush homed, that the input shaft was only half inserted into the bush, the wear on the shaft was quite evident.The installed depth of the spigot bush has no bearing on and cannot change or alter the physical or installed length of the clutch gear other than to foul the shoulder of the clutch gear splines if the bush is not installed deep enough into the crankshaft.
If you have a look into the spigot bush recess in the end of a crankshaft you will notice the hole is tapered to a point so even though the perimeter of the spigot bush has bottomed on the shoulder in the crank recess there is a deeper void in the centre.
I use grease and an old clutch gear to hydraulically remove a spigot bush. I've also heard of using wet paper balls packed into the bush instead of grease or bolts screwed into the bush or Dynabolts etc etc. To date I have never seen or been able to find any information in any Holden workshop manual regarding removal or installation of spigot bearings, therefore I believe Holden didn't regard it to be important or critical enough to bother to mention.
Too far out and as you suggest it would foul on the input shaft. (no end float)

Does this apply to every holden ever made, maybe not but I think it would just be variations on a theme.
The spigot bearings installed position is set as a match to the input shaft spigot (Obviously 100% overlap) where that position is on the crankshaft I suggest in not homed as per the drawing supplied.
Edited by Balfizar, 28 September 2015 - 09:52 PM.
#16
Posted 28 September 2015 - 11:42 PM
Interesting diagram, never seen that before. Is it GM or GM-H origin?
#17
Posted 29 September 2015 - 12:05 AM
Interesting diagram, never seen that before. Is it GM or GM-H origin?
GMH - M39434K 1988 SS Group A Volume 9 (a very rare manual indeed) perhaps why you have not seen this before and I cannot find any reference to spigot bearing in my collection ranging 1978 to 1988 as you have suggested hardly rates a mention. Not the first time GMH overlooked something. VL manuals was the first consolidation of manuals for a long time. Prior to that there was always refer to previous manuals , 1986 cars were still referencing 1971 manuals.
#18
Posted 29 September 2015 - 12:23 AM
Well that seated dimension is great info for Aussie V8 owners but unfortunately not much help for Red/Blue/Black 6 owners.
At the end of the day you say your spigot bush was driven all the way home in the crankshaft which caused the bearing surface on the end of the clutch gear to be only about 50% engaged into the spigot bush instead of 100%.
Judging by the diagram you have posted it appears there should be a gap of approx 4mm or 5mm between the end of the bush and the shoulder inside the crank. How long is a genuine spigot bush? 25mm?
#19
Posted 29 September 2015 - 12:27 PM
I am usually fitting non standard combos so am in the habit of double checking everything during fitment. I recommend it highly as it will save you from discovering you have a dud replacement part before you get too far, even with the stock stuff.
Spigot bushes do seem to vary quite a bit in height depending on where you get them from.

If you can, try to buy from your local brake and clutch bloke who has been around a while. There are apparently some bushes floating around that are made of incorrect alloy and will squeal after a while.
Press out the old one with grease and a plunge rod. This means you can reuse it another time if it's still in good condition. Never seen the point of removal methods that are destructive.
Soak the new bush overnight in oil.
Dummy fit box and bellhousing to engine without clutch. This will give you some idea of how far in you will need to insert the bush. Look through the clutch fork hole if need be.
Remove bush from oil and wipe clean. Wipe the back of the crank clean and have a feel for rough edges or burrs while you do it.
You might like to give the outside of the bush a little rub with some sandpaper but go gently if you do.
Start the bush using an alignment tool. I have a couple of whittled sticks that I use or an old input shaft from a dead box is good.

Please don't use a socket or other steel object to drive it in. If you are overly enthusiastic or inept you will damage the front of the bush. Use a wooden or plastic driver instead. Don't be too gung ho. Once close you can check progress by refitting the bellhousing and box. Go slowly and you will get it spot on.
I have had one occasion where even with the bush inserted as far as possible it was still too proud and caused binding of the input shaft. Make sure you have a couple of mm float allowance and the input shaft turns freely by hand when installed without the clutch.
Now you can install the clutch.
Refit bellhousing, box, thrust bearing and fork. Check your geometry is good.
Now you can pull it apart into small enough bits to get back into the car!
#20
Posted 29 September 2015 - 12:32 PM
Well that seated dimension is great info for Aussie V8 owners but unfortunately not much help for Red/Blue/Black 6 owners.
At the end of the day you say your spigot bush was driven all the way home in the crankshaft which caused the bearing surface on the end of the clutch gear to be only about 50% engaged into the spigot bush instead of 100%.
Judging by the diagram you have posted it appears there should be a gap of approx 4mm or 5mm between the end of the bush and the shoulder inside the crank. How long is a genuine spigot bush? 25mm?
19.11 mm
I am still thinking variations on a theme for Red/Blue/Black 6 owners.
it would not be easy but with no driveplate and a installed gearbox you would get a fair idea the correct position of the spigot bearing relative to 100% overlap on the input shaft.
Probably need an inspection camera and I don't think you could measure it. It was painful using a straight edge and depth on the verniers to measure the position of the bush when I was driving it in. (under the car with the driveplate + calculated measurement).
If the collective knowledge of this forum is missing a chapter on spigot bush installation then we have "a challenge to overcome and an opportunity to impress." (thats what my boss used to say when he was giving me a shyte job)
Every manual, Viva to LX should be scoured for this info, perhaps even wider rangeing to get the variations on a theme I have referred to.
Off you go lads give it a "red Hot go" as Brocky used to say.
#21
Posted 29 September 2015 - 12:50 PM
Variations on a theme.
#22
Posted 29 September 2015 - 05:25 PM
Here's where I'm at right now. Bought myself a new spigot. I took the clutch and pressure plate off my flywheel, and decided to dummy up the gearbox to the motor with the spigot I installed previously still in the crank.
I bolted up the gear selector and put the box to the motor and it went all the way to the dowels, some wiggling for 5 seconds and its home. I then tried to select gears and it shifted all nicely.
I'm thinking my clutch aligning was incorrect. It took me hours of hardcore wiggling to get it to mate last time and the only way it went on was by using the bolts (ouch! Yes I know, please don't sledge me for that, I was desperate).
So I bought and used a clutch aligning tool and bolted the clutch kit back on and dummy fit the gearbox to the engine again. After 20 seconds of wiggling it located on the dowels and I bolted her up. Now when I play with the selector it's changing into every gear nicely. Last time I couldn't even smash them into gear.
I knew clutches needed to be aligned closely, but are the tolerances that small between working and not working?
Just gotto pull it apart again, fix rear seal on sump, torque everything down and hopefully be good to reinstall!
#23
Posted 29 September 2015 - 05:42 PM
Clutch misalignment is only a problem until you push the clutch pedal in for the first time, after that everything self-centres.
I've cheated a couple of times before when I didn't get the clutch alignment spot on by disengaging the throwout bearing / pressure plate with a lever up through the inspection cover, but pulling it in with the bellhousing bolts is asking for trouble, if it takes that much effort than something is definitely not right.
As already mentioned, pre-fit everything, check the throwout fits the gearbox, check the clutch plate suits the input shaft and flywheel, check the spigot fits both the input shaft and crank, etc.etc.
A spare input shaft is definitely the best method of aligning a clutch, in fact an absolute necessity with multi-plate clutches as you have to align the splines of each plate to the other(s) as well.
You can grease the input shaft lightly but bear in mind whatever you use will eventually get flung out onto the friction material of the clutch plate so lubricate sparingly.
#24
Posted 29 September 2015 - 10:10 PM
Now that I have aligned the clutch and installed the box back on the engine (out of the car) it seems to shift nicely.
And another thing, this uc needed the floor cut out a little bit more due to the starfire to 6 conversion, I cut it just enough to get the shifter to bolt up, I'm wondering if I need to enlarge the hole just a little bit more so the box can sit right up in the hole / cabin (tailshaft yoke to gearbox on a slight angle).
frustrating
#25
Posted 29 September 2015 - 11:12 PM
Did you check there was no binding of the input shaft on the spigot bush?
Have you set up your pivot ball height and clutch fork angle correctly?

Create the proper clutch fork angle.
Install the ball stud onto the bellhousing.
Add a small amount of grease to the ball stud and attach the throw-out bearing to the clutch fork.
Secure the clutch fork to the ball stud.
Check the angle of the clutch fork by gently pushing against the end of the fork as the clutch pedal would until the throw out bearing touches the fingers of the pressure plate. The clutch fork angle should be within 5 to 7 degrees of parallel to the motor, angled toward the motor.
If you’re using an adjustable ball stud, screw the stud in or out to achieve the 5°-7° angle. Once you find the location, secure the lock nut.
3 user(s) are reading this topic
0 members, 3 guests, 0 anonymous users