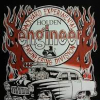
Blue 202 dizzy recurving
#1
Posted 07 August 2023 - 07:08 PM
Big fat disclaimer: up front
I am far from an expert on this subject, I am sure there are many here who can add more to this info and give input to improve your results and more importantly **** prevent anyone from doing damage to their engines as result of my backyard methods.
The only thing I have ever seen about this is in rodomo’s brilliant thread about his commodore race car, so I thought I might throw my 3 cents in
If I can add anything to that, cool.
And if anyone more knowledgeable than me can add to this, please do
I read everything I could find about this, mostly American forums on chevelle, corvette and V8 sites saying to get the advance in as soon as possible before pinging. Start the advance just after idle, and get it all in as quick as possible, quoting numbers for total as early as 2400, and then the usual 3000ish.
I fiddled and ended up with mine in at 2000. No good. Not pinging, but no power up top.
Just been back into it to correct my now obvious balls up, and aim for closer to 3000.
The important thing here is to know what the engine needs first, and I am still learning there.
I took pics this time to show some stuff.
Here she is in the vice. I lined up the rotor arm with no.1 lead in the dizz before removing it from engine.
Then you can stick it back in in the same spot with no disasters.
you have one of these electronic numbers, line up the 6 points inside the dizz right on to be sure.
Take note, too. I write it all down and draw pictures too
Once you’re done, it’ll be easier to get it back in right then.
#2
Posted 07 August 2023 - 07:34 PM
After removing cap and module cover (on left) and inner 6 pointed reluctor wheel with circlip,here is what you are left with.
Alll through, make sure you take note op all the circlips and shims and washers to get get them back together in the right order later.
That is more important than I want to rave about ..
I have skipped a tiny bit here, not being a professional photographer and all,
the key to the next step is to remove the vacuum advance module, that is a tricky bit, especially the putting it back in place part.
You will thank me for that advice later, it is a bastard getting it back in place later on. After a few goes, it comes easy, though
so the whole magnetic coil ( the outside 6 pointed thingo) can rotate into position so the screw s line up for removing.
Some of these are Allan screw heads
Some of the inner 6 pointed reluctor wheels have a slip-in round pin to locate them.
Take it easy when you lever this feller off the shaft and take note in case this this pin is there
Are the pictures there?
#3
Posted 07 August 2023 - 07:54 PM
#4
Posted 07 August 2023 - 07:59 PM
#5
Posted 07 August 2023 - 08:06 PM
Here’s what you are left with.

Those are the springs that need tweaking
#6
Posted 07 August 2023 - 08:10 PM
remove the shims that go with it there.
** do not lose track of those shims and where they came from **
Ah shit.

I am no good at this
#7
Posted 07 August 2023 - 08:15 PM
Anyhow
Punch the shaft out fron the bottom of the dizz, not too rough now
And you will be left with this in your hot little hand

#8
Posted 07 August 2023 - 09:06 PM
You’ll need a timing light and a bit of paper at least, and a pencil
If your balancer doesn’t have marks up to 30/40, you’ll need an adjustable timing light so you can map out your curve
If you don’t have a target, there isn’t much point having a go at this. The oldjohnno page has a guide to what sort of engine needs what sort of curve and total advance numbers to aim for. I am experimenting within what I think are safe limits to find something close to optimamal for my engine. Might not get it perfect though
Anyone with some more knowledge than me here is more than more than welcome to add some knowledge to this right now
#9
Posted 07 August 2023 - 09:36 PM
Sent from my SM-G781B using Tapatalk
#10
Posted 07 August 2023 - 09:47 PM
But before I make a total tit of myself, I had a target of a high 20 degrees initial from the engine builder based on the cam and the head it was being fitted under
Whatever your initial needs to be for off idle response and low end power, combined with whatever your total or all in timing needs to be will tell you how much mechanical advance the dizz needs to bring in.
Standard dizzys are roughly 6 degrees at idle and a total of mid 30s this all changes with improvements in general engine hotness, cam spec, compression and so on. So my target at this point is 20 and 32. Right or wrong until advised by cleverer types. I don’t mind at all pulling dizzy and having another go at this, which makes this all an ok process for me, but that may be understandably a pain in the arse for someone else

Spin the shaft upside down and this is the view
The two slots the red bushes are in are the ones That limit the travel of the twist of the bitsnup above and limit the total timing.If you want 20 and 32 for example, that’s 12 on the balancer, *** But only 6 on the distributor ***
Most recommend a blob of weld in there to be filed down until the right amount of movement in the advance mechanism is achieved. In my case 6
I have filled mine with jb weld, still spinning around after several months and hanging in there, I don’t guarantee or promise It is the right thing to do so don’t copy me, I may be proven wrong yet
#11
Posted 07 August 2023 - 09:51 PM
this is hard work for a computer dummy
Gotta give it to all the blokes before me who write stuff up
There’s funnier backyard stuff to come yet
You can all laugh and point at funny old me then hhahha
#12
Posted 07 August 2023 - 10:05 PM
Either reassemble entire dizz and run it up in the car with timing light, or try this bench top wonder

If you grip end of the rotating shaft in the softjaws in vice and jig up protractor as shown,
You can twist the top assembly against the springs and measure (roughly) how much you are getting
This is probably better done before it is back in the housing, easier to pull out and give a few more rubs with file
to creep up on the number you are after
I wanted 6 to give me 12
20init 32 tot on balancer
If you want 10 initial and 34 total (on balancer) that’s 24
12 in dizzy
On the you beaut protractor
I double checked on running motor afterwards
Was willing to pull it and fix though
Needs a bit patience, this way
Save a few bucks, say proudly that you did it yourself if you like that sort of thing
#13
Posted 07 August 2023 - 10:44 PM
you can see all over the place this one from a corvair site

Here’s a curve with 5 initial and 33 ish total. The left side first bit up to 1200 rpm is rather result of the primary spring acting on both spinning no weights on its own. At 1200 rpm, the secondary spring comes into effect, and adds to the spring load slowing the curve rate up to the point where the total advance is limited. The kink in the curve at 1200 rom shows the 2 springs adding together
This is my before and after graph

First attempt on the left, this weeks re-do on the right. Yes I can see the 30 total on the first and 32 on the second
I blame that on the balancer markings beindpg difficult to see and my eyes being difficult to see through, but I did check the second time over and over after I noticed that hahahh
I am sure there is maybe just a leetle beet of less-than-lab spec accuracy in my methods, but I figure that it’s better than not doing any checking at all
#14
Posted 07 August 2023 - 11:06 PM

You can see how rpt he secondary spring has a longer loop inboard which does nothing until the first spring is stretched by the weights heading outward enough to reach the point where the second spring starts to stretch too.
One spring’s resistance for a while, until both spring’s resistance is in play.
My first graph shows that there is not much change in the line where the second spring comes in
The previous time to that result, ai noticed the second spring was not even being stretched at all, due to the tiny 6degree amount of movement in the mechanism not reaching the end of the long loop.
The fix for this is to give the outer spring post a tweak, so it at least was in the game. How much of a tweak?
That was a guess, and the pencil graph shows the result. Be prepared do do it again. And maybe again again.
#15
Posted 07 August 2023 - 11:26 PM
Saw first graph, couldn’t hear pinging so all good.
Later found differing opinions, saying “on this motor and others I have seen, too fast timing curve killed top end power”
Ah shit here we go now it’s in my head I have to know, so we try it. Engine does seem happier, but once all the tuning falls into place around the new big change, I will know for sure.

These are the outer spring posts which can be bent to increase or decrease the spring tension which brings on the changes in the graphs. You can see I have numbered the weights with a text a because I have developed a duffer’s habit of not remembering things I swore I’d never forget 25 seconds before. It’s important to keep each spring in it’s place as well, as the lengths between posts measured different for each spring
#16
Posted 07 August 2023 - 11:55 PM

By altering the spring posts to alter the spring tensions the left line became the right.
I bent the primary spring post outwards by 20thou, which held the weights in a little bit stronger, causing the curve to begin to rise a few revs later as expected.(I’d hoped) By rights, it should tilt the line over a bit, too acting like a stronger spring. It’s either too subtle to notice, or my first lot of measurements aren’t accurate enough to show it properly. Probably the latter there.
The second spring I thought needed a bigger adjustment and god a 60thou tweak outwards, reducing the slack in the long loop and coming in earlier, as shown by the point in the line where the two lines bend. It’s also more apparent it is having a heavier spring effect by the angle of the line. Holds off the point of total advance until 3200ish now.
Cool
#17
Posted 08 August 2023 - 12:21 AM
So back into the vice, grabbing it by the main body this time set up the protractor meter and rigged up the patented vacuum gauge suck-ometer
Just a tube between vac canister and gauge with a t- piece and another tube into the gob.
One with a yellow sticker with 6 on it ind 230 stamped into the arm
Started moving @ 5”
6degrees @7”
8degrees @ 9”
Max 11degrees @ 11”
The one I am using no sticker left but 214 stamped on arm
Started @ 7”
4degrees @ 9”
Max 8degrees @11”
Distributor degrees, so double these for balancer degrees
Staying with the same one. Not really sure what to do with these figures yet, or really have a decent understanding what the engine would want vacuum advance wise
Hope it’s of some use to someone out there, anyway

Suckometer vac canister testing equipment
#18
Posted 08 August 2023 - 01:06 AM
And a couple of top tips I left out.
If there’s anything I’ve missed, please jump in and correct me
Check for extra shims beneath the rotating assembly, between it and the alloy body
They can stick to the underside of the rotating plate could and drop off unnoticed while you’re carrying it around
Watch where you put the round pickup coil, it is super magnetic and will pick up untold amounts of metal swarf and chips and crap off your workbench

Make sure the screws for the coil are in the right holes. The vac canister rod won’t go in if they aren’t right
Going through the process of screwing it down and shimming the gaps only to find it won’t go in will make you swear a lot
Don’t forget to give the moving parts some grease. I have used the white silicone heat sink grease, which stayed put pretty well after a few months use. Might not be the ideal thing, though. Better ideas would be good for me, too
#19
Posted 08 August 2023 - 01:25 AM
Beneath the little felt pad,mothered is a circlip and a washer. I can’t thing of any better way to get it off except to gently prise
it off of the baseplate. Leave felt in and they won’t fly out. Weights need to come off too, probably mark them to go back in same spot.
When putting top part back onto shaft, I couldn’t fit anything down that tiny hole to re-attach circlip, but had success dropping in in and pushing it on with a
plastic biro tube
Pickup coil next, get screws in and leave them a bit loose. Then centre star shaped reluctor wheel.

Needs to be centralised with shims of some sort and tightened down. You’ll know if it’s not right, the pointys will hit each other
Make sure you forget to put the rotor button back in, whack the thing back in right where you found it
Those 6 triangular points make it real easy to line up number one for a reference before pulling it out, saves headaches when putting it back
#20
Posted 08 August 2023 - 06:51 AM
Sent from my SM-G781B using Tapatalk
#21
Posted 08 August 2023 - 02:08 PM
Awesome write up, thanks for the detail. Will be my go-to when I have a crack at this
#22
Posted 08 August 2023 - 03:47 PM
I have been trying to invite some of the clever guys around here to chime in and add anything extra advice to all this, and I still hope they will
There’s a lot of cautionary tales out there too about the potential for engine damage, because pinging is not always possible to hear, especially with a rowdy motor with a loud exhaust. Piston damage, pounding out big end bearings and probably a few other things can occur
Klevliend, I think you were talking about putting some more initial timing into yours?
Every car I have owned since discovering the idea seems to like a couple of degrees more initial timing.
My Mitsubishi work van loves it. But, too much and she’ll ping, and the top end power seems to suffer a bit. Mileage seems to take a bit of a hit, too
So then I put the timing back down again
I suppose there’s not too much harm in trying bumping the dizzy a little bit to see if the off the mark throttle response improves,
probably a smart move really, to see whether it’s worth doing the modification. That would still be an improvement even if the springs were left alone
This is what I’d like to do to my van, initial higher, and leave the total where it’s supposed to be
Just don’t load it up too much up a steep hill and rev the hell out it
Here’s a couple of links to the ones I bookmarked for my reference
http://www.gofastfor...ion/advance.htm
http://www.s26261265...rews/timing.htm
Better explanations of the real techy theory in those
#23
Posted 08 August 2023 - 04:12 PM
Reading your description certainly gives me confidence in having a go. frOcken koala stamp mate!
Sent from my iPad using Tapatalk
#24
Posted 08 August 2023 - 08:58 PM
Your cam is a dynotec
People tell me I know fark nothing
I correct them and say I know fark all
#25
Posted 09 August 2023 - 09:43 AM
It’s made me keen to have a look & play with the one I’m going to put in my refreshed motor 😁
As for removing the clip to release the top part of the shaft , Fuzzypumper on here did a good write Up years back that I followed to referb a few & one of his suggestions was when driving off the drive gear it also dislodges the wire clip that retains to top part of the shaft.
I leave the felt in the shaft to contain the clip and a safer precaution is to place a plastic bag over the top of the distributor to catch all of the stray parts
https://www.gmh-tora...ei-distributor/
1 user(s) are reading this topic
0 members, 1 guests, 0 anonymous users